A 3D-printed car is an automobile built using 3D-printing methods, where its components are constructed layer by layer using specialized material and equipment. A promising application of the additive manufacturing production process, this approach allows for greater customization and sustainability, transforming the way automobiles are produced and designed.
What Is a 3D-Printed Car?
A 3D-printed car is a vehicle that is made using additive manufacturing, where its components are constructed layer by layer using various materials like plastics, metals or composites.
Car companies have been implementing this technology, in some capacity, for years now. In fact, 3D-printing industry veteran and former executive at additive manufacturing firm Stratasys Michael Bourque estimates that 100 percent of car design today is done with 3D printing. “They’re in it,” he said of the industry, “and they’re doing amazing things.”
At this point, applications of 3D printing in the automotive industry are limited to prototypes and individual parts. When it comes to the mass production of complete and fully functional vehicles, traditional manufacturing methods remain the standard. And it will likely be a while before that changes.
What Are 3D-Printed Cars Made Of?
One of the more common materials used to make 3D-printed car parts are thermoplastics like acrylonitrile butadiene styrene (ABS) and polylactic acid (PLA), which are used for prototyping and creating lightweight, non-structural components. Additive manufacturing expert Tuan Tranpham said the majority of 3D-printed car parts over the years have been cosmetic — “it’s a gear knob, it’s a decorative logo,” he explained.
That’s beginning to change, though. Processes such as selective laser melting (SLM) and direct metal laser sintering (DMLS) are helping produce parts using metals like aluminum, titanium and stainless steel, which are used for more critical components like engine brackets and pistons. And ceramics can be used for components that need to be resistant to high temperatures and wear, such as vent valves and fuel pumps.
Once the parts are printed, they are assembled to the larger vehicle using both traditional fastening methods (screws and bolts) and, in some cases, 3D-printed connectors.
3D-Printed Car Examples
While it promises to bring efficiency and sustainability to the automotive industry, 3D-printing technology is not currently capable of producing an entire working car on its own. Still, several companies have unveiled vehicles with the majority of their components — and even main functional parts like the framework — manufactured using 3D-printing technology.
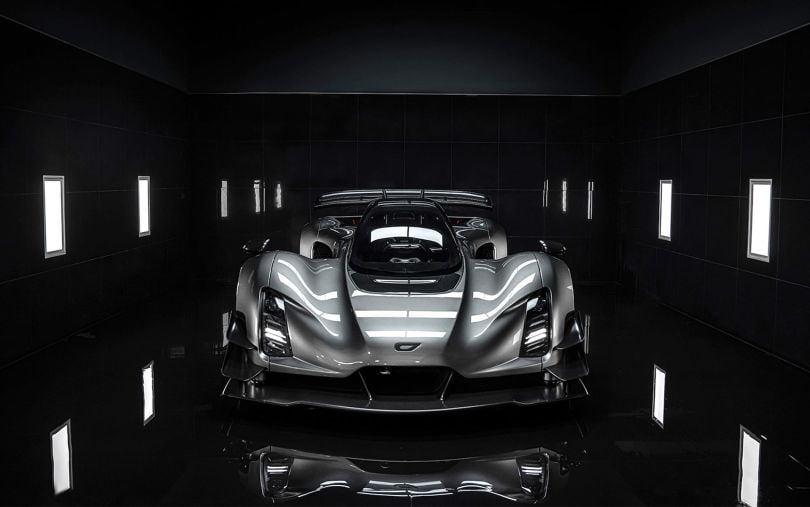
1. Czinger Vehicles’ 21c
Hailed as the world’s first 3D-printed hypercar, the 21C is the flagship product of sports car manufacturer Czinger Vehicles. The entire chassis is designed, made and assembled using 3D-printing technology, according to founder Kevin Czinger, as is the entire suspension system, except for things like shock absorbers. The exhaust elements of the car’s engine are 3D-printed as well. With a price tag of $2 million, the 21C can reach 60 miles per hour in just 1.8 seconds, hitting top speeds of 253 miles per hour. The car is considered to be the next iteration of the Blade, another groundbreaking 3D-printed car also made by Czinger and his other company Divergent Technologies.
- Manufacturer: Czinger Vehicles
- Printed materials: Metal
- Speed: 253 miles per hour
- Price: $2 million
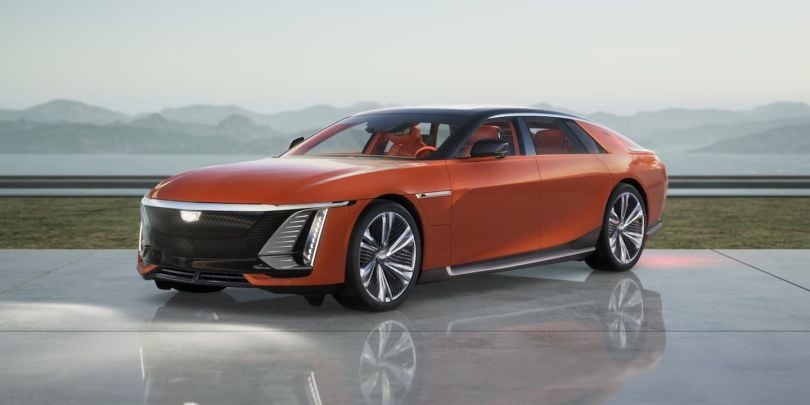
2. GM’s Celestiq
Celestiq is the newest Cadillac model. The electric sedan is said to contain more 3D-printed components than any other vehicle previously produced by General Motors — 115 to be exact, some of which are structural and others cosmetic. Its steering wheel trim, for example, is one massive metal 3D print, requiring no specific tooling to produce, which means it can be highly modified. GM has begun training technicians to support drivers of the Celestiq as the model is set for a limited release. The car’s price reportedly starts at $340,000, but will likely retail for more than $400,000 with add-ons and customizations.
- Manufacturer: General Motors
- Printed materials: Polymer and metal
- Speed: Top speeds have not been disclosed, but Cadillac says the car can go from zero to 60 miles per hour in 3.8 seconds
- Price: Minimum $340,000
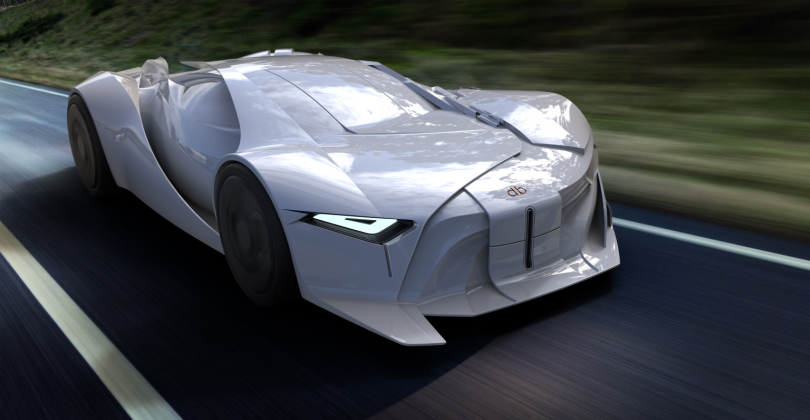
3. Massivit 3D Printing’s David Bowie Car
Featured at the 2019 Festival Automobile International exhibition, the David Bowie tribute concept car was produced by Israeli company Massivit 3D Printing in collaboration with renowned car designer Takumi Yamamoto, who is a fan of the late rock icon. The car was manufactured in just two months, and was made entirely of Dimengel, an instantly curing acrylic gel that can produce lightweight, hollow 3D-printed models. While not fully drivable, the David Bowie Tribute Car is a 1:1 scale prototype meant to show what is possible with 3D printing in the automotive industry.
- Manufacturer: Massivit 3D Printing
- Printed materials: Dimengel acrylic gel
- Speed: Not driveable
- Price: Not for sale
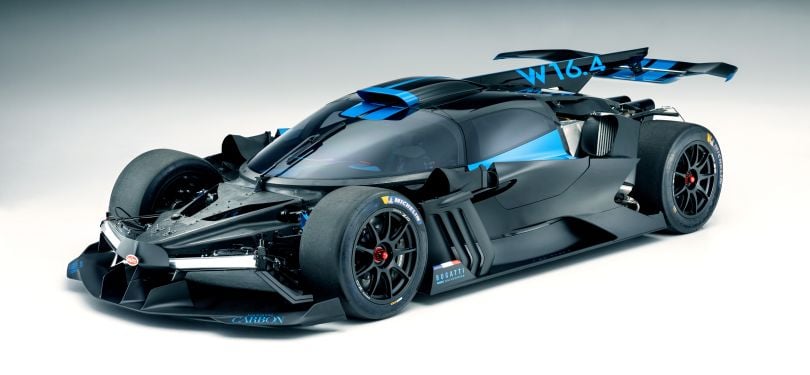
4. Bugatti’s Bolide
Luxury car manufacturer Bugatti was one of the first high-end automotive companies to adopt 3D-printing technology, using SLM to print parts out of titanium, carbon and ceramic since 2018. And it incorporated several 3D-printed parts into its new hypercar, the Bolide, including brake components, brackets and a titanium pushrod suspension system to make it lighter. The Bolide can hit top speeds of 310 miles per hour, making it among the fastest cars in the world. With only 40 Bolides in existence, the model comes with a hefty price tag of $4.7 million.
- Manufacturer: Bugatti
- Printed materials: Metal and ceramics
- Speed: 310 miles per hour
- Price: Approx. $4.7 million
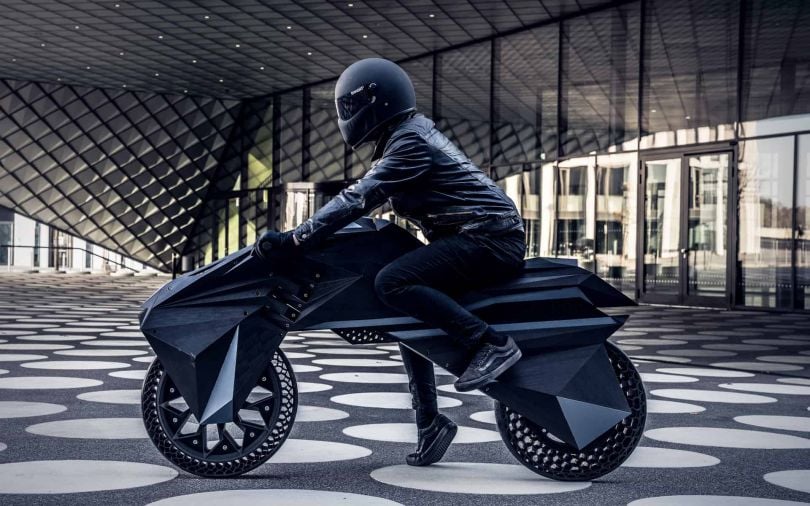
5. BigRep’s NERA
Created by Germany-based company BigRep, NERA (short for New-Era) is reportedly the world’s first fully 3D-printed electric motorcycle. While it is not technically a car, the functional prototype pushes the boundaries of vehicle engineering and production, offering everything from custom-fitted seating to airless tires. With the exception of its battery, motor, cable and control systems, all of NERA’s parts are 3D-printed using PLA, Pro FLEX (a flexible thermoplastic material), and ProHT, which is capable of withstanding high temperatures. BigRep claims the bike went from initial idea to its maiden voyage in just 12 weeks.
- Manufacturer: BigRep
- Printed materials: PLA, Pro FLEX, PETG and ProHT
- Speed: BigRep claims its airless tires are rated for 38 miles per hour
- Price: Not currently for sale
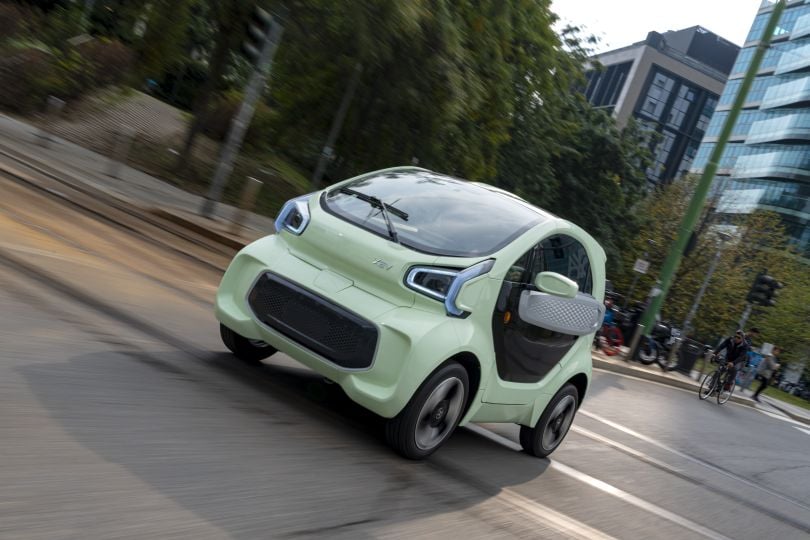
6. XEV’s Yoyo
Developed by electric car manufacturer XEV and filament manufacturer Polymaker, the Yoyo is one of the only 3D-printed cars to have successfully been released to the public. The compact electric vehicle is designed for an urban environment, with a battery range of 90 miles and a top speed of about 55 miles per hour. Excluding parts like tires, seats, windows and chassis, both the interior and exterior of the vehicle have been 3D-printed using ABS. The Yoyo is only available for sale in Italy, where XEV is based, and costs a minimum of 13,900 euros (about $14,500).
- Manufacturer: XEV
- Printed materials: ABS
- Speed: 55 miles per hour
- Price: Approx. $14,500
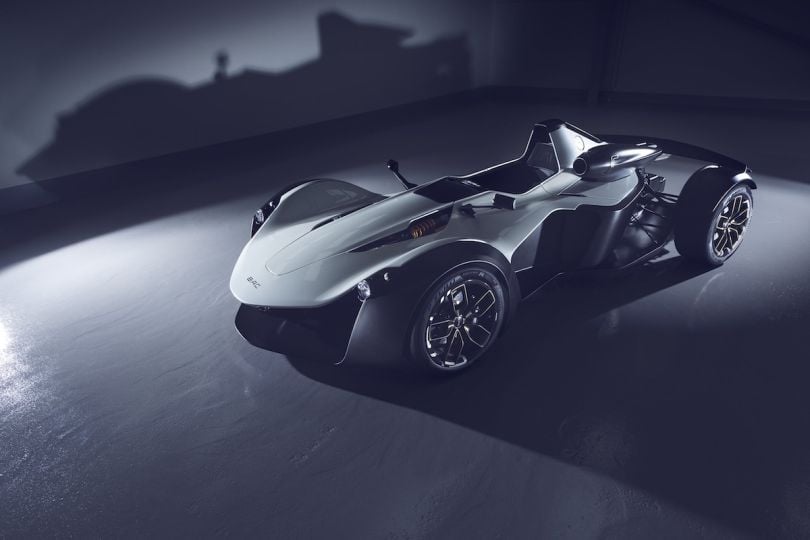
7. BAC’s Mono R
Briggs Automotive Company (BAC) teamed up with 3D-printing company DSM to produce the BAC Mono R. The model features a graphene-enhanced carbon fiber body, resulting in a sturdy structure. However, the car still weighs a record-low 560 kilograms (roughly 1,234 pounds) thanks to its 3D-printed parts, including steering wheel grips and air inlets. The duo of DSM and BAC continue to look for ways to make the Mono R even more lightweight, such as incorporating hollow structures into the car’s design.
- Manufacturer: BAC
- Printed materials: Graphene-enhanced carbon fiber
- Speed: 170 miles per hour
- Price: Approx. $240,000
3D-Printed Car Part Examples
Additive manufacturing isn’t only used by luxury and experimental car makers. Everyday brands like Ford and BMW are 3D-printing some of their parts too. Having the ability to design and print parts onsite means these companies don’t have to wait for the long lead times required in traditional machining, and they can easily experiment and iterate their designs.
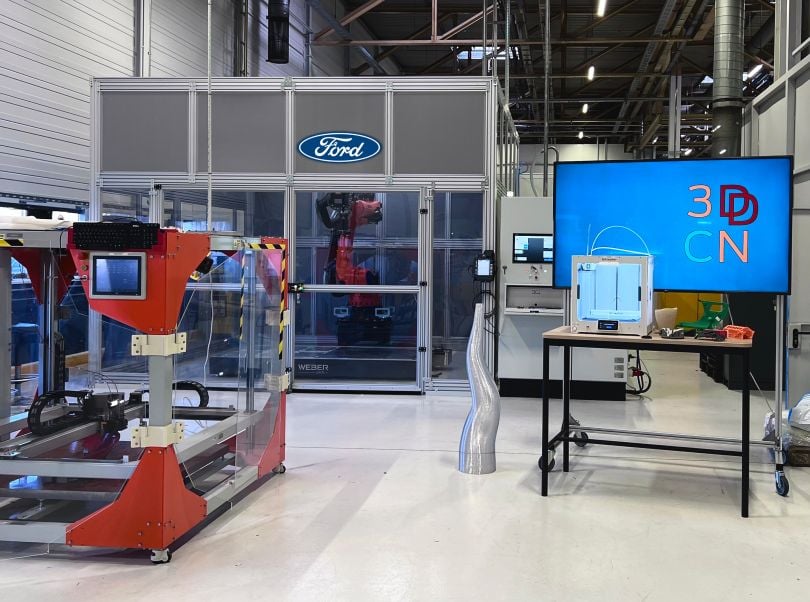
1. Ford
As the company that introduced the world to modern car manufacturing, it makes sense that Ford is a trailblazer in 3D printing among the automotive industry. In addition to some of the tools, jigs and fixtures needed to actually manufacture its cars, the company 3D prints its prototypes and some of the parts that actually go in the vehicles themselves. Its 2020 Shelby GT500, for example, has two structural 3D-printed brake components, which passed all of Ford’s performance standards and requirements. And in 2019 the company produced the largest metal part ever made using 3D printing — an aluminum intake manifold for the engine of a Ford F-150. In 2023, the company also opened a new 3D printing center to support the production of its first electric vehicle built in Europe.
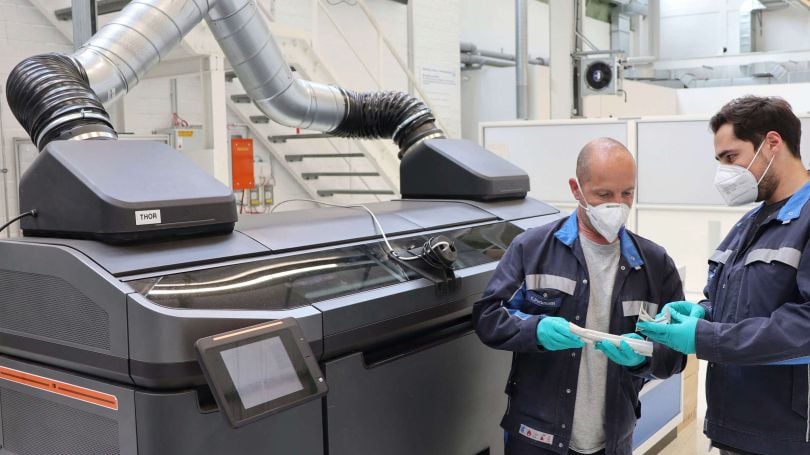
2. Volkswagen
Volkswagen was among the automotive industry’s earliest adopters of binder jetting, an additive manufacturing process that makes 3D printing with metal cheaper and more productive. The company has aimed to produce up to 100,000 components using 3D-printing technology each year by 2025 at its main plant in Wolfsburg, Germany, several of which for the A-pillar and T-Roc convertible are already in the process of being certified.
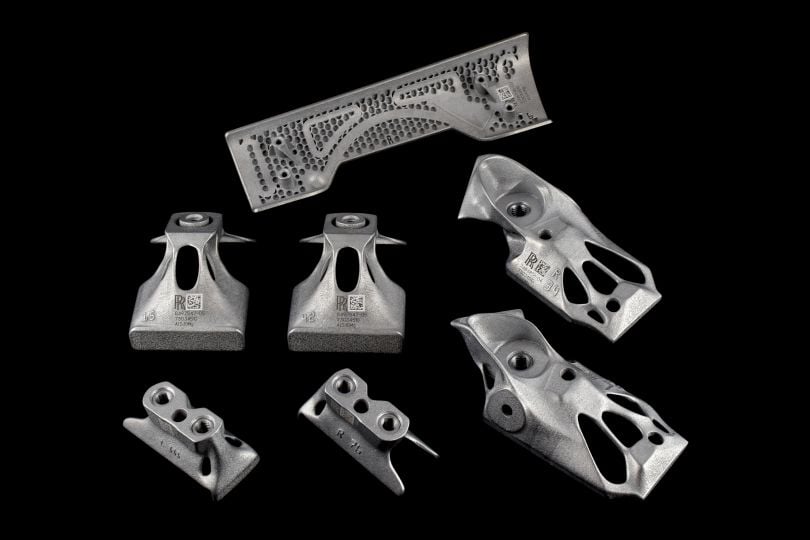
3. BMW
For years, BMW has been using 3D-printing technology for small series production in its luxury cars that are made to order, producing small metal components for the vehicles’ bodies and passenger cells through laser beam melting, as well as polymer parts through multi-jet fusion and selective laser sintering. The company also uses the technology to prototype and test parts during the design process of all its cars. It even opened a couple of fully automated production lines in Germany, where it reportedly ships millions of 3D-printed components daily.
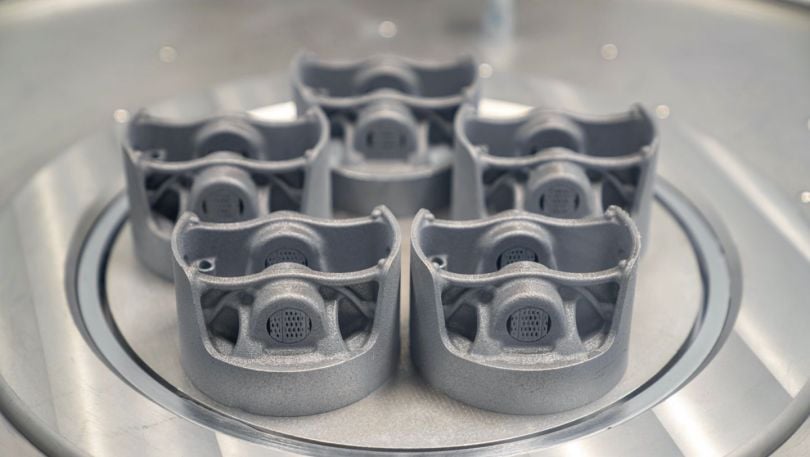
4. Porsche
Porsche has been using additive manufacturing in both its prototyping phase and the production of several parts — even going so far as to invest in 3D-printing specialist INTAMSYS through its venture arm. In 2020, the company developed a way to 3D print metal pistons that weigh 10 percent less than their traditional counterparts and incorporate cooling channels in their crown, a design that would not have been possible using conventional manufacturing methods, according to Porsche. These pistons are now incorporated into its 911 flagship model, the GT2 RS. Porsche also 3D prints components for its classic car models that have parts no longer in production.
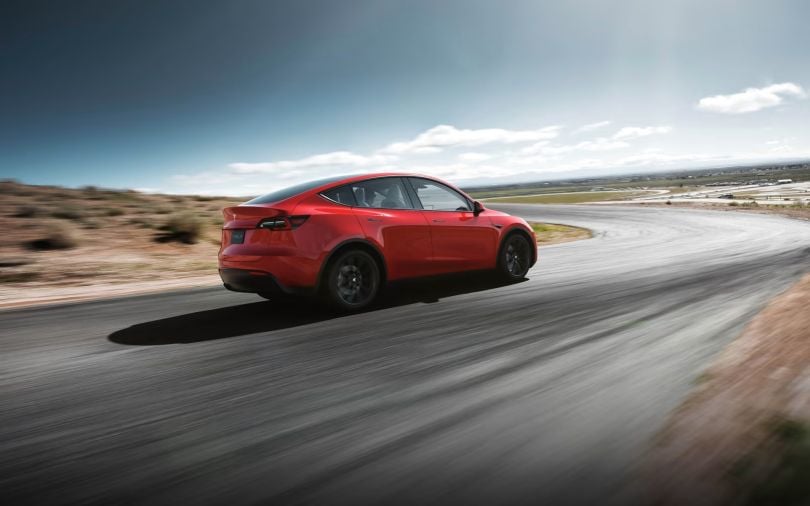
5. Tesla
Tesla has secretly experimented with 3D printing the bodies of some of its Model Y cars, using ultra-high pressure presses to mold large sub-units of the car and then snapping them together. While Tesla has not confirmed any of this, anonymous sources told Reuters that the technique combines 3D printing and industrial sand, where Tesla uses a mold comprising 3D-printed solid sand cores inside. The sand is then removed after casting, leaving a hollow subframe that does not need to be welded together, The Verge further explained. The process could be a more efficient means of production, and give the company more wiggle room in terms of design.
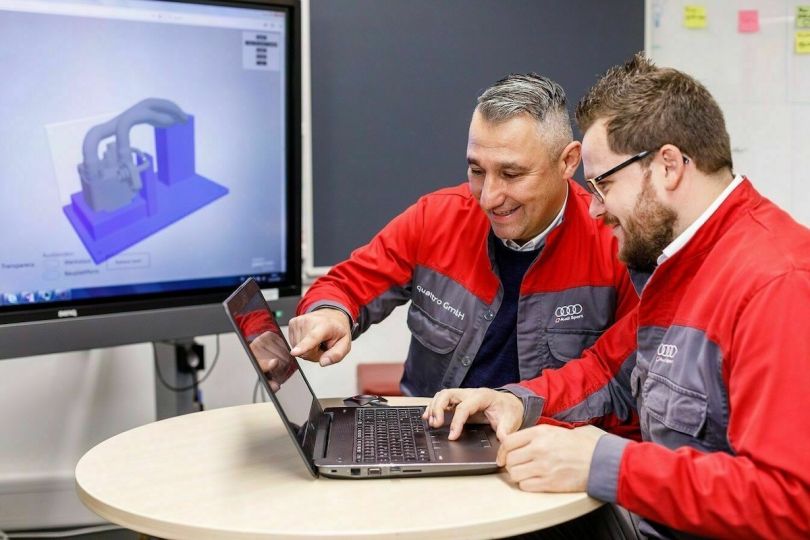
6. Audi
Under the Audi umbrella, Audi Sport has used 3D printing to make its processes much more efficient and cost-effective. The company has paired Trincklemate’s Fixturemate software with 3D printing to quickly generate parts unique to the fully electric E-Tron GT, cutting down on time and resources that otherwise would’ve been needed for production. In addition, Audi Sport has adopted UltiMaker S series 3D printers to create car parts in-house, shaving production costs by as much as 80 percent.
Why 3D Print Cars?
Using additive manufacturing in both design prototypes and functional vehicles helps automakers save time and money. Because these components can be made in-house, they can be changed and improved upon quickly. And companies don’t have to wait for parts to be made and shipped from somewhere else.
The process also produces significantly less waste than traditional machining, according to Tranpham. “That’s the whole notion of additive,” he said. “You build it from the ground up, you don’t chip away from a big block down to what you need. It’s totally reversed thinking.”
When Will 3D-Printed Cars Go Mainstream?
The mainstream adoption of 3D-printed parts in the automotive industry depends on several factors, including technological advancements and improvements in quality and speed. Additive manufacturing may be a faster and more cost-effective option when it comes to producing just one prototype or a few specialty cars, but things get trickier as volume grows.
“The automotive industry is really a numbers game,” Bryan Murphy, who heads the Oklahoma Additive Manufacturing Center, told Built In. Many car companies produce millions of vehicles a year, with each consisting of thousands of complex parts made up of different materials. With this many moving parts, speed, cost-efficiency and quality are the three most important things in auto manufacturing.
Meanwhile, 3D printing is “tremendously slow,” according to industry veteran Bourque. And the technology is still limited in the materials it can work with and the speed at which it can print. Plus, the quality of the product isn’t always up to the standards required in a road-safe machine.
“3-D printing is really, really tough. In order to make a safe and quality product, it is really hard, it requires a lot of R&D, and it involves a lot of quality monitoring on the back end,” Murphy continued. “At this stage in additive manufacturing’s life, it’s really less economical to 3D print the whole car than it is traditional manufacturing, where you have set processes in place, set approval for materials.”
So how long will it be before we have 3D-printed Fords or Toyotas rolling off the assembly lines?
“We’re probably another 10, maybe 20 years from something like that,” Murphy said. “We’re a ways off.”
Frequently Asked Questions
Are there any 3D-printed cars?
Yes, but they are simply prototypes or concept cars that have been 3D-printed to varying degrees. For now, the average consumer cannot go to a dealership and purchase an entirely 3D-printed car. But many major car makers have incorporated 3D printing into their design and manufacturing process to produce certain parts.
How much does it cost to 3D print a car?
There is no standard cost for 3D printing a car, as it can vary widely depending on factors like the size and complexity of the car parts being printed, as well as the material and technology used. Some estimates run between tens of thousands to hundreds of thousands of dollars.
How long does it take to make a 3D-printed car?
The time it takes to 3D-print a car can vary significantly depending on several factors, including the size and complexity of the car parts being printed, as well as the material and technology used. Printing only car parts or small prototypes can take several hours or days. So producing an entire, fully functional car would likely take weeks, or even months.
How strong are 3D-printed car parts?
The strength of 3D-printed car parts depends on the materials they’re made of. However, some 3D-printed car parts are strong enough to have been used in NASCAR race models.
Are 3D-printed cars cheaper?
While 3D printing car parts — especially DIY solutions — can be cheap, entirely 3D-printed cars are not cheaper than traditionally made vehicles. The price of a 3D-printed car can also vary between models.