The Future of 3D Printing
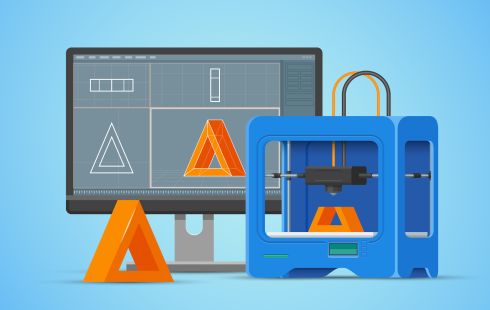
3D printing uses specialized equipment to create solid, three-dimensional objects from a digital file. The practice has been around since the 1980s, when Charles W. Hull invented the process and created the first 3D-printed part. Since then, the field of 3D printing has grown exponentially and holds countless possibilities.
3D printing is a process that uses computer-aided design, or CAD, to create objects layer by layer. 3D printing is commonly used in manufacturing and automotive industries, where tools and parts are made using 3D printers.
As the capabilities of 3D printing continue to grow, so does its value: By 2029, the 3D printing industry is estimated to reach a value of $84 billion. This growth means we are bound to interact with products — and even homes and buildings — made with 3D printing.
3D printing is also shaking up the healthcare industry. In 2020, the COVID-19 pandemic overwhelmed hospitals and increased the need for personal protective equipment. Many healthcare facilities turned to 3D printing to supply their staff with much-needed protective equipment, as well as the parts to fix their ventilators. Large corporations, startups and even high school students with 3D printers stepped up to the plate and answered the call. 3D printing will not only change how we make PPE and medical equipment, but also streamline prosthetics and implants.
Although 3D printing is not necessarily new, there are some who still wonder what 3D printing is and how it works. Here’s a guide to understanding 3D printing.
In short, 3D printers use CAD to create 3D objects from a variety of materials, like molten plastic or powders. 3D printers can come in a variety of shapes and sizes ranging from equipment that can fit on a desk to large construction models used in the making of 3D-printed houses. There are three main types of 3D printers and each uses a slightly different method.
3D printers aren’t like those magical boxes in sci-fi shows. Rather, the printers — which act somewhat similarly to traditional 2D inkjet printers — use a layering method to create the desired object. They work from the ground up and pile on layer after layer until the object looks exactly like it was envisioned.
The flexibility, accuracy and speed of 3D printers make them a promising tool for the future of manufacturing. Today, many 3D printers are used for what is called rapid prototyping.
Companies all over the world now employ 3D printers to create their prototypes in a matter of hours, instead of wasting months of time and potentially millions of dollars in research and development. In fact, some businesses claim that 3D printers make the prototyping process 10 times faster and five times cheaper than the normal R&D processes.
3D printers can fill a role in virtually almost every industry. They’re not just being used for prototyping. Many 3D printers are being tasked with printing finished products. The construction industry is actually using this futuristic printing method to print complete homes. Schools all over the world are using 3D printers to bring hands-on learning to the classroom by printing off three-dimensional dinosaur bones and robotics pieces. The flexibility and adaptability of 3D printing technology makes it a game-changer for any industry.
3D printers have extreme flexibility for what can be printed with them. For instance, they can use plastics to print rigid materials, like sunglasses. They can also create flexible objects, including phone cases or bike handles, using a hybrid rubber and plastic powder. Some 3D printers even have the ability to print with carbon fiber and metallic powders for extremely strong industrial products. Here are a few of the common applications 3D printing is used for.
3D printing provides companies with a low-risk, low-cost and fast method of producing prototypes that allow them to test a new product’s efficiency and ramp up development without the need for expensive models or proprietary tools. Taken a step further, companies across many industries utilize 3D printing for rapid manufacturing, allowing them to save costs when producing small batches or short runs of custom manufacturing.
3D printing has become more functional and precise over time, making it possible for proprietary or inaccessible parts to be created and acquired so a product can be produced on schedule. Additionally, machines and devices wear down over time and may be in need of swift repair, which 3D printing produces a streamlined solution to.
Like functional parts, tools also wear down over time and may become inaccessible, obsolete or expensive to replace. 3D printing allows tools to be easily produced and replaced for multiple applications with high durability and reusability.
While 3D printing may not be able to replace all forms of manufacturing, it does present an inexpensive solution to producing models for visualizing concepts in 3D. From consumer product visualizations to architectural models, medical models and educational tools. As 3D printing costs fall and continue to become more accessible, 3D printing is opening new doors for modeling applications.
3D printing is part of the additive manufacturing family and uses similar methods to a traditional inkjet printer — albeit in 3D. Additive manufacturing describes the process of creating something in layers, adding material continuously until the final design is complete. This term most often refers to molding and 3D printing.
It takes a combination of top-of-the-line software, powder-like materials and precision tools to create a three-dimensional object from scratch. Below are a few of the main steps 3D printers take to bring ideas to life.
The first step of any 3D printing process is 3D modeling. To maximize precision — and because 3D printers can’t magically guess what you want to print — all objects have to be designed in a 3D modeling software. Some designs are too intricate and detailed for traditional manufacturing methods. That’s where CAD software comes in.
Modeling allows printers to customize their product down to the tiniest detail. The 3D modeling software’s ability to allow for precision designs is why 3D printing is being hailed as a true game changer in many industries. This modeling software is especially important to an industry, like dentistry, where labs are using 3D software to design teeth aligners that precisely fit to the individual. It’s also vital to the space industry, where they use the software to design some of the most intricate parts of a rocketship.
Once a model is created, it’s time to “slice” it. Since 3D printers cannot conceptualize the concept of three dimensions, like humans, engineers need to slice the model into layers in order for the printer to create the final product.
Slicing software takes scans of each layer of a model and will tell the printer how to move in order to recreate that layer. Slicers also tell 3D printers where to “fill” a model. This fill gives a 3D printed object internal lattices and columns that help shape and strengthen the object. Once the model is sliced, it’s sent off to the 3D printer for the actual printing process.
When the modeling and slicing of a 3D object is completed, it’s time for the 3D printer to finally take over. The printer acts generally the same as a traditional inkjet printer in the direct 3D printing process, where a nozzle moves back and forth while dispensing a wax or plastic-like polymer layer-by-layer, waiting for that layer to dry, then adding the next level. It essentially adds hundreds or thousands of 2D prints on top of one another to make a three-dimensional object.
There are a variety of different materials that a printer uses in order to recreate an object to the best of its abilities. Here are some examples:
Plastic material that is easy to shape and tough to break. The same material that LEGOs are made out of.
Carbon fiber is used to create objects that need to be strong, but also extremely lightweight.
These printable materials are still in the experimental stage and can be used for printing electric circuits without the need for wires. This is a useful material for wearable technology.
Flexible filaments produce prints that are bendable, yet tough. These materials can be used to print anything from wristwatches to phone covers.
Metal filaments are made of finely ground metals and polymer glue. They can come in steel, brass, bronze and copper in order to get the true look and feel of a metal object.
These filaments contain finely ground wood powder mixed with polymer glue. These are obviously used to print wooden-looking objects and can look like a lighter or darker wood depending on the temperature of the printer.
The 3D printing process takes anywhere from a few hours for really simple prints, like a box or a ball, to days or weeks for much larger detailed projects, like a full-sized home.
here are also different types of 3D printers depending on the size, detail and scope of a project. Each different type of printer will vary slightly on how an object gets printed.
FDM is probably the most widely used form of 3D printing. It’s incredibly useful for manufacturing prototypes and models with plastic.
SLA is a fast prototyping printing type that is best suited for printing in intricate detail. The printer uses an ultraviolet laser to craft the objects within hours.
DLP is one of the oldest forms of 3D printing. DLP uses lamps to produce prints at higher speeds than SLA printing because the layers dry in seconds.
CLIP is amongst the faster processes that use Vat Photopolymerisation. The CLIP process utilizes Digital Light Synthesis technology to project a sequence of UV images across a cross-section of a 3D printed part, resulting in a precisely controlled curing process. The part is then baked in a thermal bath or oven, causing several chemical reactions that allow the part to harden.
Material Jetting applies droplets of material through a small diameter nozzle layer-by-layer to build a platform, which becomes hardened by UV light.
Binder Jetting utilizes a powder base material layered evenly along with a liquid binder, which is applied through jet nozzles to act as an adhesive for the powder particles.
FDM, also known as Fused Filament Fabrication (FFF), works by unwinding a plastic filament from a spool and flowing through a heated nozzle in horizontal and vertical directions, forming the object immediately as the melted material hardens.
A form of Powder Bed Fusion, SLS fuses small particles of powder together by use of a high-power laser to create a three-dimensional shape. The laser scans each layer on a powder bed and selectively fuses them, then lowering the powder bed by one thickness and repeating the process through completion.
Another form of Powder Bed Fusion, MJF uses a sweeping arm to deposit powder and an inkjet-equipped arm to apply binder selectively on top. Next, a detailing agent is applied around the detailing agent for precision. Finally, thermal energy is applied to cause a chemical reaction. Direct Metal Laser Sintering (DMLS) also utilizes this same process but with metal powder specifically.
Sheet Lamination binds material in sheets through external force and welds them together through layered ultrasonic welding. The sheets are then milled in a CNC machine to form the object’s shape.
Directed Energy Deposition is common in the metal industry and operates by a 3D printing apparatus attached to a multi-axis robotic arm with a nozzle for applying metal powder. The powder is applied to a surface and energy source, which then melts the material to form a solid object.
3D printing has permeated almost every single sector and has offered some innovative solutions to challenges all over the world. Here are a few cool examples of how 3D printing is changing the future.
3D printed food seems like something out of the Jetsons or too good to be true. In fact, if it can be pureed, it can be safely printed. Like something out of a sci-fi show, 3D printers layer on real pureed ingredients, like chicken and carrots, in order to recreate the foods we know and love.
3D printed food is entirely safe to eat as long as the printer is completely cleaned and working properly. You might want to order your meal ahead though. 3D food printers are still relatively slow. For example, a detailed piece of chocolate takes about 15 to 20 minutes to print. Even so, we’ve seen printers craft everything from burgers to pizza and even gingerbread houses using this mind-blowing technology.
Nonprofits and cities all over the world are turning to 3D printing to solve the global homeless crisis. New Story, a nonprofit dedicated to creating better living conditions, built the first 3D-printed community in Mexico. Using a 33-foot long printer, New Story is able to churn out a 500 square-foot home, complete with walls, windows and two bedrooms in just 24 hours. So far, New Story has created mini 3D-printed home neighborhoods in Mexico, Haiti, El Salvador and Bolivia, with more than 2,000 homes being 100 percent 3D printed.
In the near future, we’ll see 3D printers create working organs for those waiting for transplants. Instead of the traditional organ donation process, doctors and engineers are teaming up to develop the next wave of medical technology that can create hearts, kidneys and livers from scratch.
In this process, organs are first 3D modeled using the exact specifications of the recipient’s body, then a combination of living cells and polymer gel (better known as bioink) are printed off layer-by-layer to create a living human organ. This breakthrough technology has the ability to change the medical industry as we know it and reduce the drastically high number of patients on the organ donation waitlist in the United States.
3D printing offers several additional revolutionary means of improving quality-of-life for patients while making solutions more accessible to healthcare providers From components for surgical machines to N95 masks and ventilators. Perhaps most impressively, 3D printing technology has even fast-tracked production and durability of prosthetics while reducing costs, like how GE Additive produced over 10,000 hip replacements through 3D printing from 2007 through 2018.
Will the future of space travel rely on 3D-printed rockets? Companies, like Relativity Space, think so. The company claims that it can 3D print a working rocket in just a few days and with one hundred times fewer parts than a normal shuttle. The company’s first conceptualized rockets, the Terran 1 and Terran R, will only take 60 days from the start of printing to the launch into space. The rocket will be custom-printed using a proprietary alloy metal that maximizes payload capacity and minimizes assembly time.
Not only are 3D printed materials easier to manufacture quickly and at lower costs but 3D printing also provides a way to reduce the total number of parts that need to be welded together while also significantly reducing weight and increasing strength. Another famous example is GE Aviation’s LEAP engine, which uses 3D printed Cobalt-chrome fuel nozzles that weigh 25 percent less and are five times as strong as traditionally manufactured nozzles.
3D printing has been utilized in the automotive industry for many years, allowing companies to shorten design and production cycles while lowering the amount of stock needed to have on hand. Spare parts, tools, jigs and fixtures can all be produced on an as-needed basis while providing flexibility that would have been unimaginable to previous generations.
Additionally, 3D printing provides a way for automotive enthusiasts to customize their vehicles or restore old cars with parts that are no longer in production. Automotive repair shops can even utilize 3D printing when faced with unusual repair requests.
Consumer products, without a digital or electronic build quality, such as clothing, eyewear, jewelry and more, can all be mass-produced through 3D printing. While various other products can have their body or frame manufactured through 3D printing, any item that can be produced within a mold can also be produced through 3D printing.
3D printing is capable of making the manufacturing process of complex parts more streamlined thanks to software programming. This often means it is a more affordable option in some industries.
Other factors that contribute to the affordability of 3D printing are the materials used. 3D printing can utilize low-cost plastics and concrete that are easily accessible. Also, because there is no need for a mold in 3D printing, that’s another cost taken off the table.
3D printing is ideal for quick prototyping of products because it can be done in house in small runs. This allows manufacturers to work out bugs and make changes to products faster than a typical production process. Alterations to products can easily be made through CAD while the manufacturing cost stays the same.
Despite plastics and metals being commonly used in the 3D printing industry, there are a host of other options to choose from. The advantage means speciality parts and products can be made with specific materials like water-absorbing plastic, nitinol, gold and carbon fiber. Speciality materials like this allow for properties such as high heat resistance, water repellency and strength.
A downside to building an object up layer by layer, is that this can affect the durability and strength of the object. Of course, the strength of 3D printing relies heavily on what materials are used; metals and concrete will always be some of the strongest materials used in 3D printing.
Although CAD is often an accessible and accurate way to design, there can be errors. Accuracy with 3D printing is dependent on the techniques and printers use. For example, some smaller 3D printers, like desktop models, can wear out easily. This means that as the production of a design goes on, the products made later on may vary from the first batch.
Another pitfall of 3D printing is the work required to finish up a product. This might include sanding or smoothing out an object, heat treatment or removing support struts. Post-processing of 3D printed products can sometimes lead to additional costs.