When your mission is unprecedented, sometimes that means inventing a whole new toolkit.
Relativity Space is no doubt flying uncharted skies. The L.A.-based aerospace startup aims to build and launch into orbit the world’s first entirely 3D-printed rocket. To do so, it has already achieved a monumental first in the process: the company has built what it claims to be the world’s largest metal 3D printer.
Because even though 3D printers have come a long way, it's not possible to print a seven-foot-wide, 105-foot-tall rocket that can withstand the extreme heat and stress of a space launch with a consumer-grade machine that's used to print DIY toys.
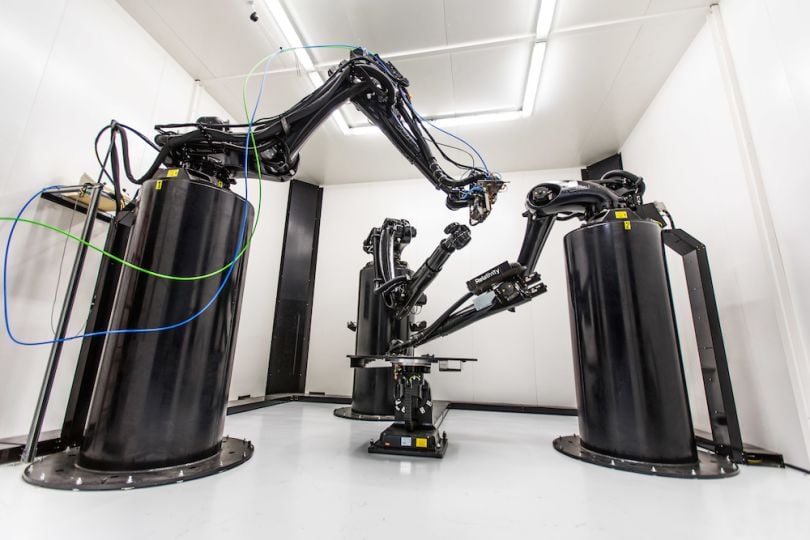
An Astronomical Printing Job
Meet the Largest Metal 3D Printer on Earth
Relativity Space’s room-filling 3D printer — dubbed Stargate, a reference to the classic sci-fi strategy game StarCraft — includes three robotic arms, each tall enough to dwarf the average adult. Not that you’d want to be nearby while it’s torching alloys into malleability. One arm is outfitted with a deposition head, through which aluminum-alloy wire feeds into the path of an ultra-powerful laser. The arm then steers the material, layer by layer, into the precise shape of a propellant tank, booster or whichever component is on the day's to-build list.
Simultaneously, the other two arms perform post-processing and inspection functions, handling operations like “tank polishing, surface removal, checking for abnormalities or verifying that a finished geometry is what we intended it to be,” says co-founder Jordan Noone, a SpaceX veteran who started the company in 2016 with former USC classmate and Blue Origin alum Tim Ellis.
Propelling 3D Manufacturing
The engine that will blast the rocket skyward is also completely 3D-printed. Relativity Space builds its engines using a process called direct metal laser sintering (DMLS): the printer constructs a given part out of powdered metal, which sits on a bed that ever-so-gradually lowers after each blast of molding heat until the form is completed.
Unlike the groundbreaking Stargate, DMLS is not uncommon in space-centric manufacturing.
“It’s a pretty tried-and-true process that’s getting fairly codified across most aerospace companies at this point,” Noone says, though Relativity Space appears to have the process down to an exceptional degree.
The rocket’s thrust chamber assembly is comprised of just three parts. Apollo mission engines back in the space-race days, by comparison, had some 5,600.
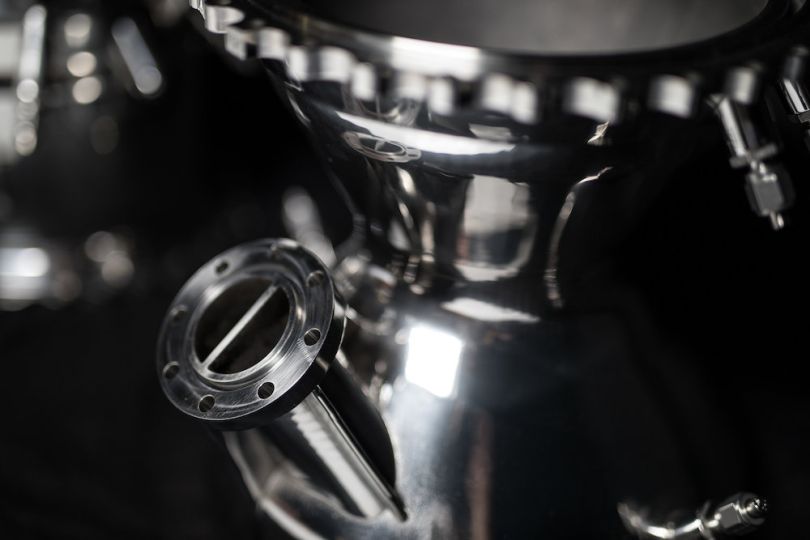
2020: A 3D Space Odyssey
That kind of optimization, and the quick-change agility afforded by additive manufacturing, is how Relativity Space hopes to differentiate itself from traditional rocket-building.
“There’s a huge barrier of entry to changing or iterating on a traditional manufacturing device,” Noone says, “and by introducing printing by default for the entire product, you maintain the ability to change things quickly and be flexible.”
How quick and flexible? The goal is to print and launch a new design in just 60 days. That kind of speed and adaptability will cut the cost of rocket flights by a huge margin — more than 80 percent, the company predicts. Noone and Ellis want to launch satellites and other small-to-midsize payloads into orbit by 2020.
Another major factor in the push toward that goal is data collection. Unlike traditional manufacturing, the Stargate printer monitors with hyper-precision each quality-determining variable throughout the entire build-out process.
“You're actually collecting data on every single point on the vehicle, and every single point of a printed part,” Noone says. “You understand what heat went into it, what the temperature was at, how quickly it cooled.”
“It’s about getting to a future where we actually have faster rates of progress as we make more and more complicated products,” he adds.
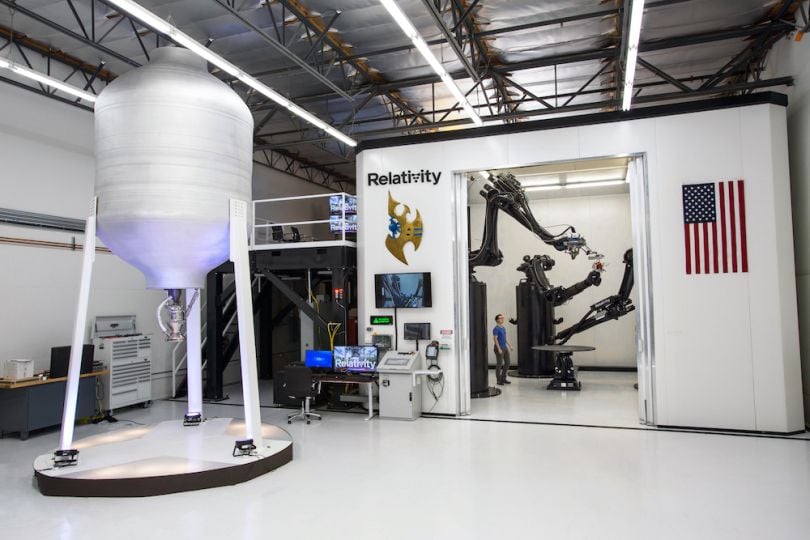
On Target for Off-Planet
Besides its 3D-printer colossus, Relativity Space has plenty more pieces in place as it eyes that future: the startup has amassed more than $45 million in funding, including seed-round investment from Mark Cuban; it has launched more than 200 engine tests from the NASA-owned site it leases at Stennis Space Center; it has acquired some celebrated former SpaceX talent; and it has even secured a launchpad at perhaps the most iconic aerospace site in the world, Florida’s Cape Canaveral.
“It’s extremely flattering to have that opportunity,” says Noone, who notes that Relativity Space’s launchpad complex boasts some “Apollo heritage” in that it’s the same complex where NASA once ran static firing tests for propulsion engines used during the historic spaceflight program.
If the company’s near-term goal seems ambitious, Relativity’s long-term objective is an absolute moonshot — or, more accurately, a Mars shot. The startup aims to one day build a completely automated 3D-rocket-printing factory on the Red Planet. Because why not?
The launch market of satellites and imaging technology is “really the backbone for developing technology that’ll be used for off-planet manufacturing and plenty of other use cases,” Noone says.
Tech types love to issue future forecasts, but it doesn’t get much more forward-looking than that.
The 3D Printing Market
This year’s edition of the influential Wohlers Report projects that additive manufacturing will grow to a $35.6 billion industry by 2024, and commercial aerospace manufacturing has emerged as a key growth driver. But industries like homebuilding, car-making, medical supply, footwear and even food are fast embracing 3D. Here are several companies whose applications are fit to print.
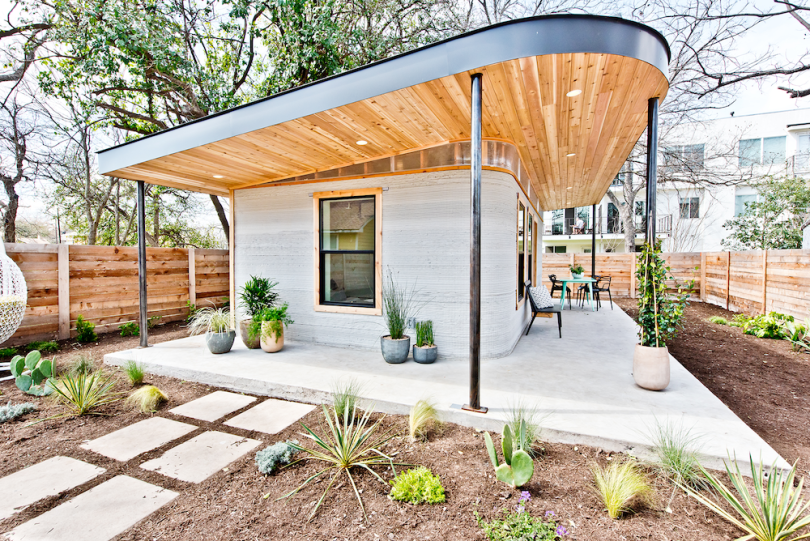
ICON
3D-PRINTED HOUSES
While habitation on Mars still requires solving some pesky surface-condition issues, the Earth faces more urgent housing challenges. Experts say 3D printing centers could help alleviate homelessness by providing eminently affordable housing.
The homebuilding startup behind the first-ever 3D-printed house, ICON uses 3D printing to build houses — not just prefab housing components, but entire homes. The company has announced multiple housing projects this year alone that include a partnership with Cielo to “print” affordable, sustainable units in Austin, Texas, where ICON is headquartered; a 3D-printed-home design contest with 3Strands; and “the world’s first 3D-printed community,” which breaks ground this year in Latin America and will be built in partnership with housing nonprofit New Story.
All three projects will employ the Vulcan II, a tablet-controlled, gantry-style printer that uses ICON’s proprietary cement-based material mix, dubbed Lavacrete, to build structures. As a gauge of Vulcan’s potential, ICON constructed its proof-of-concept prototype house using the printer in under 24 hours for less than $4,000. The company says Vulcan II will be available to order in 2020.
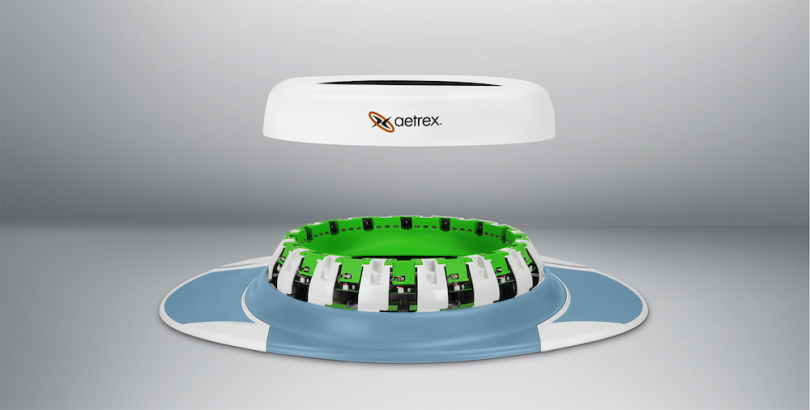
AETREX WORLDWIDE
THE FUTURE OF FOOTWEAR
3D imaging is now the standard in orthotics exams, but 3D technology increasingly is a staple in shoe design as well. Aetrex Worldwide, which acquired 3D-printing foot-support startup Sols in 2017, combines the two. A computer vision-enhanced foot scanner named Albert draws up an ideal blueprint for each customer, then a printer kicks out the customized orthotic. In fact, most of the major footwear brands have at least dipped a toe into 3D. In 2017, Adidas introduced its Futurecraft 4D shoe that was made using a process developed by Carbon. And Formlabs developed a material for New Balance called Rebound Resin, a springy-but-strong base that reportedly performs better than foam.
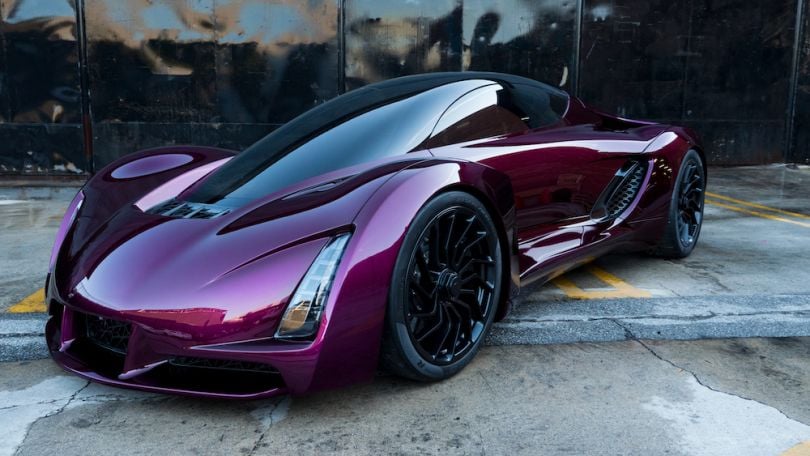
DIVERGENT 3D
3D PRINTS YOU CAN DRIVE
Divergent’s 3D-printed supercar, the Blade prototype, looks very much like a car-guy car with its Lamborghini-style scissor doors and painfully sleek aerodynamics. But don’t mistake that wavy, futuristic design for mere concept-car showiness. Blade’s parts are shaped just so in order to optimize strengths and loads, not just to look cool. (It’s not uncommon for software-designed, 3D-printed industrial parts to have organic, almost plant-like shapes; they often distribute weight and stress better than their more traditional-looking counterparts.)
Like Relativity Space’s engine, the Blade was made using a DMLS process. And similar to Relativity’s rocket and ICON’s homes, the aim was to 3D-print a product, or as much of one as possible, rather than a product’s many individual parts. Both the chassis and body of the car are made with additive manufacturing. Since debuting Blade in 2015 and unveiling intermittent updates, the L.A.-based outfit has also partnered with the automaker behind Peugeot to bring its 3D printing processes to production facilities.
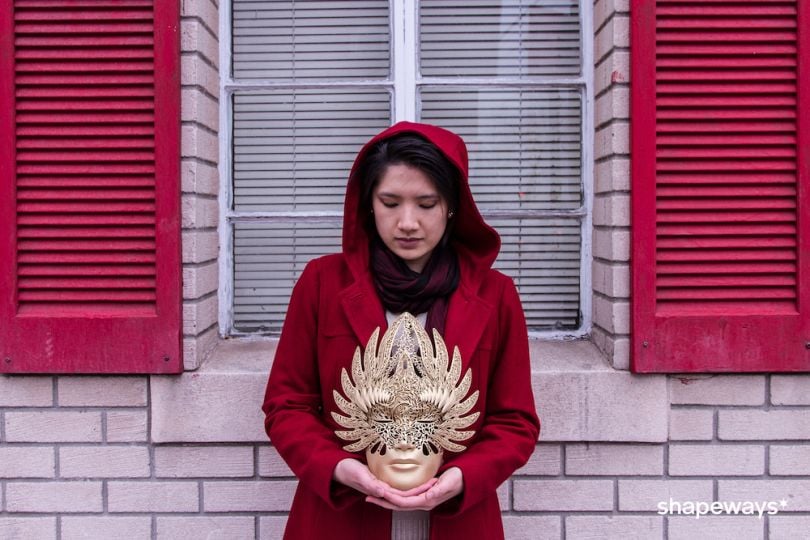
SHAPEWAYS
JEWELRY & HOUSEWARES
This 3D-printing marketplace does everything from manufacturing prostheses to delivering prototypes for virtual reality gear, but it’s best known as a printer-on-demand for consumers and independent craftspeople. 3D-printing is a no-brainer for jewelry, housewares and decorative objects, thanks to its capacity for intricate detailing. Shapeways — which recently integrated with Etsy — lets anyone submit DIY 3D models and pick a material and finish. It then prints objects in far better quality than a consumer-grade printer can muster.
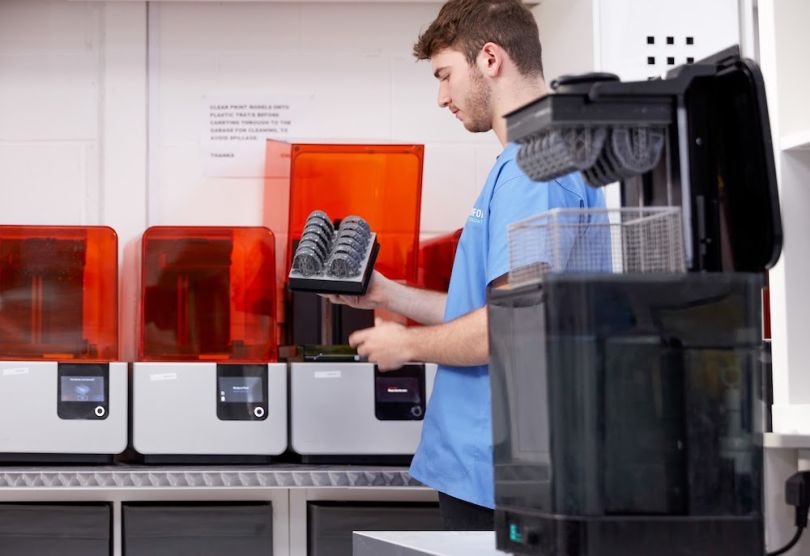
FORMLABS
BETTER DENTAL MATERIALS
Since 3D printing allows for complex control over details in small-size pieces, it’s become a go-to for manufacturers of small medical implants and devices, like hearing aids and dental accessories. Bell cow startup Formlabs is emblematic of the latter. Founded by three then-students at the MIT Media Lab, the company supplies its popular Form printers to Ashford Orthodontics, the UK’s largest orthodontics lab, which uses them to print bridge models, surgical guides, retainers, dentures and other dental devices at scale.
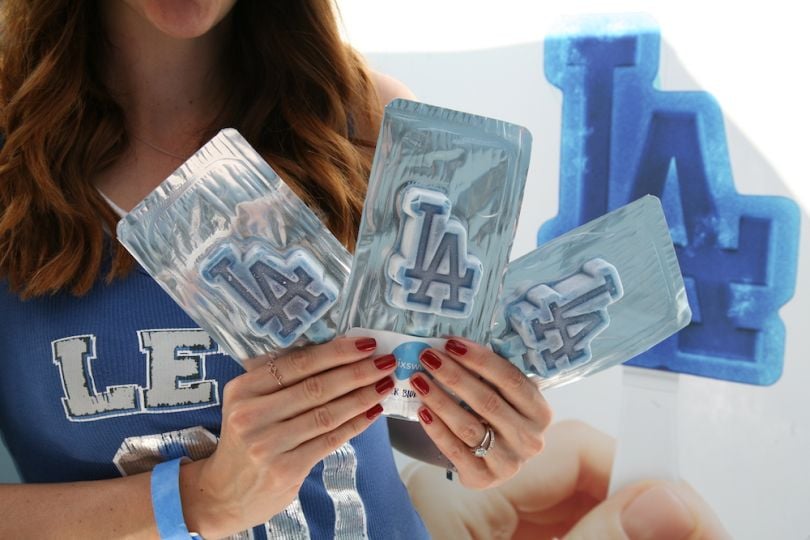
PIXSWEET
THE THIRD DIMENSION OF FOOD
From elaborate biomimicking pastries to architectural chocolates, tech-friendly bakers have been exploring the decorative powers of 3D-printing in desserts and sweets for years now. One notable entry is Pixsweet, which lets customers design and print up custom 3D ice pops. But it’s not all sugar bombs. Natural Machines’ Foodini, for instance, is specifically designed to print food using fresh natural ingredients. Spinach dinosaurs, anyone?
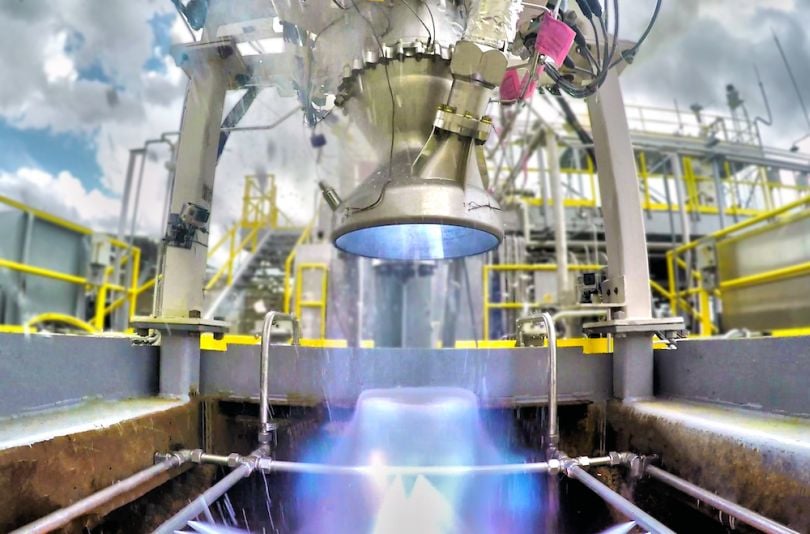
Getting Closer To Blastoff
When Additive Manufacturing Works Best
While 3D printing has delivered on many fronts, it hasn’t yet disrupted large-volume manufacturing across the board in quite the way some true believers anticipated it would. High costs and relatively slow turnarounds have kept additive manufacturing mostly the province of prototyping and a narrow range of small parts fabrication. Step-by-step, though, steady advancements are improving that outlook.
Formlabs’ aforementioned Form printers, for example, are well-regarded as affordable yet high-performing stereolithography options. And Desktop Metal has spearheaded a binder jetting process that combines multiple steps with each pass its printhead makes over the powder bed: depositing and compacting metal powder, dropping binding agents and building and drying interface layers. Translation: it can manufacture metal parts very quickly.
Also, 3D-forward “flexible factories” are increasingly attractive to industries that value adaptability.
“The ability to change quickly and rely less on any fixed infrastructure is extremely valuable for industries that want to move quickly, that want design flexibility,” Noone says.
“A high adoption of 3D printing enables a completely different operational structure for a company.”
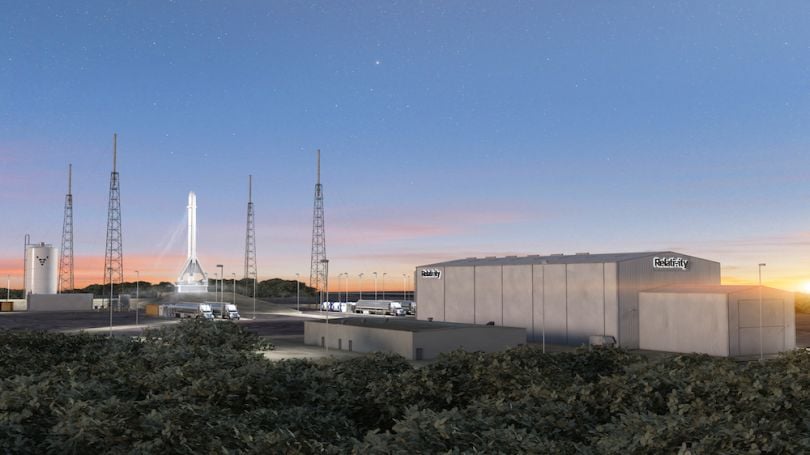
Making a Material Impact
One hurdle toward larger 3D-printing adoption might stem from a lingering underestimation of its present-day capabilities. These are not brittle plastic feedstocks. The fact that Noone trusts an additive-manufactured rocket to withstand the intense thermal pressures of a blast into space illustrates how well suited the process now is for high-performance alloys. He likens Relativity Space’s printing operation — essentially, high heat followed by fast cooling — to that of a blacksmith quenching a sword.
“It parallels the printing process, where you have this local heat source,” Noone says. “But it's so local and so small you actually have this dramatic cooling rate, which can strengthen the metal much more than traditional manufacturing techniques like casting, or even high-end metal techniques like wrought material or forging.”
That kind of technology is galaxies away from the stuff of amateur maker labs, and it remains a bedrock in Relativity Space’s ultra-ambitious mission. The end goal of off-planet automated rocket-building “is something we're always getting closer and closer to,” said Noone, “and it’s very much the guiding light for the company still today.”
Images via Shutterstock, social media and featured companies