A business student walks into a 3D printing lab.
It sounds like the setup to a joke. But as the director of MakerLab, a 3D printing lab in the Gies Business School at the University of Illinois at Urbana-Champaign, Dr. Vishal Sachdev actually sees that happen all the time.
“The first question that people have is, ‘What do I do with [the printers]?’” he told Built In. “Most people are not really used to making things. They’re used to buying things.”
Back in 2012, Sachdev had heard of 3D printing, but hadn’t actually done much of it himself. He was a business professor, and 3D printing typically was considered the province of engineers. Ultimately, it’s a manufacturing technique, not a business proposition. Right?
3D Printing Applications and Examples
- Aeronautics and space travel
- Construction
- Fashion
- Food
- Healthcare
Not according to Sachdev’s colleague, Dr. Aric Rindfleisch. He convinced Sachdev that 3D printing also had major business implications. It could shift entire business models, transform supply chains and alter consumer behavior. If people could print physical objects from their desktops, maybe they would start relating to them differently.
Sachdev was intrigued. In 2013, he and Rindfleisch opened MakerLab, the first 3D printing lab based in a business school.
Though 3D printing presents some scalability issues — it’s not as fast as comparable methods, especially for large batches — it has impacted a variety of fields. We rounded up a few of the ways it’s being used in industries from fashion to food.
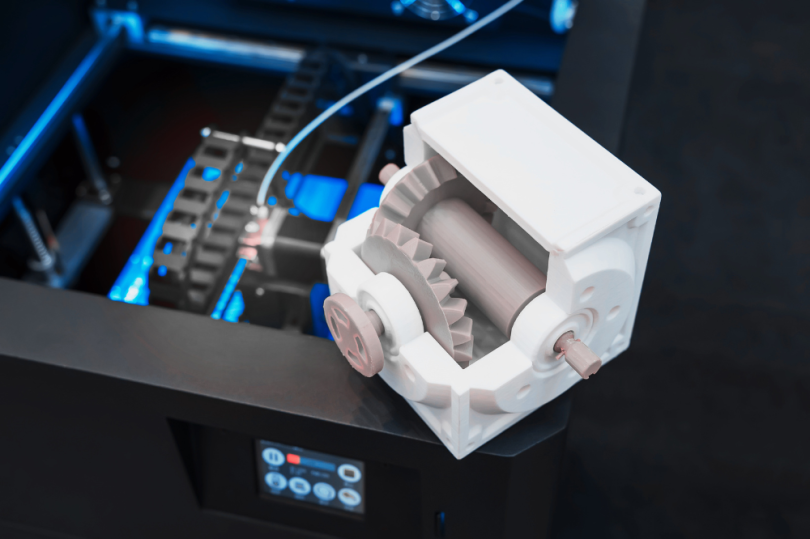
3D Printing in Aeronautics and Space Travel
Usually, mass-producing a complex machine means manufacturing a million different parts. 3D-printing changes that. As early 3D-printing innovator Avi Reichenstal said in his Ted Talk, “The printer doesn’t care whether it makes the most rudimentary or most complex shape.” In other words, the technology makes intricate designs simple to produce.
This has been a boon to the aeronautics industry. These days, the process of manufacturing jet and rocket engines often involves 3D printed parts.
Location: Atlanta, Georgia
GE Aviation’s LEAP engine, used in Boeing and Airbus aircraft, requires 19 metal jet fuel nozzles. Once upon a time, each nozzle was assembled from 20 different pieces, each forged in its own way. 3D-printing streamlined the process — now, nozzles can be printed all in one piece, and require no assembly.
As of 2021, GE has printed more than 100,000 nozzles in the new way, and is at work to integrate 3D printing further into GE’s manufacturing processes.
Location: Longbeach, California
With the goal of eventually housing humans on Mars, Relativity Space is an aerospace company creating rockets and satellite launch services, and believes 3D printing is the future of manufacturing. Relativity Space’s rockets use extensive 3D printing technology, allowing vessels to be created within 60 days and even have reusable engines.
Terran 1, the world’s first entirely 3D-printed rocket, is designed for astral deployment and resupply endeavors. Terran R, the world’s first reusable 3D-printed rocket, will be able to launch over 20,000 kilograms worth of payload into Earth’s orbit. Terran 1’s first demo launch is scheduled for summer 2022, while Terran R’s is scheduled for 2024.
Location: Washington, D.C.
The unmanned Orion capsule, which NASA developed for its Artmes I moon mission, was created with a newly lightweight engine thanks to 100 3D-printed parts. Each will be printed from a special plastic filament, engineered with space travel in mind. The ultra-durable material is cheaper and lighter than metal, which makes the capsule more aerodynamic.
The plastic is also less vulnerable to static. “In space… materials will build up a charge,” Scott Sevcik, Vice President of Stratasys Manufacturing Solutions, told Reuters. “If that was to shock the electronics on a spacecraft, there could be significant damage.”
Location: Hawthorne, California
SpaceX’s guiding vision — making commercial space travel as accessible as an Earthbound flight — would make no sense without 3D printing. SpaceX has long experimented with the manufacturing technique, which could radically reduce the cost of rocket engines. First, the company made Falcon 9, a transport rocket whose engine has a 3D-printed valve. Then came the Dragon passenger spacecraft, whose SuperDraco engines are completely 3D printed. As of 2022, Falcon 9 has completed over 150 launches, and Dragon completed over 30 with successful deliveries to the ISS.
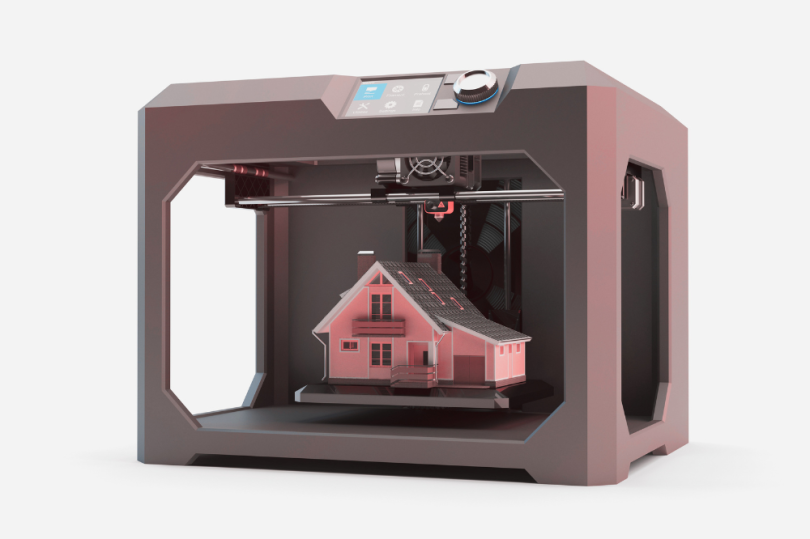
3D Printing in Construction
A hundred years from now, the phrase “printing a house” might have replaced “building a house” in common parlance. Already, a handful of companies have developed the technology and materials to 3D-print custom cement housing in as little as 24 hours. It’s cheap, too — sometimes as little as $10,000.
That’s just one of the ways 3D printing has shaken the foundations of the construction industry. Some institutions are experimenting with adobe printing, or using 3D-printed models to illustrate new architectural visions.
Location: Austin, Texas
ICON is a construction company changing the game of architectural manufacturing with its robotic 3D printing technology. Using its Vulcan construction system, ICON has developed 3D-printed structures ranging from homes and full-sized neighborhoods to U.S. military training barracks. In its most ambitious project, the company is collaborating with NASA to create 3D-printed livable habitats in preparation for expeditions to Mars.
Location: Elkridge, Maryland
Part of the PERI Group, Peri 3D Construction uses autonomous robots to create 3D-printed houses, notably the first-ever printed home to appear in Germany. The company’s structures are created using concrete layering techniques from its COBOD BOD2 printer. Each printer’s dimensions can be customized to the specifics of a project and do not need to be repeatedly recalibrated, saving significant time during construction. In 2022, Peri 3D Construction collaborated with Habitat for Humanity to complete construction of a single-family home in Arizona, which has now been moved into.
Location: Ogden, Utah
It can be hard to visualize a construction project based solely on a blueprint or a computer simulation. WhiteClouds offers an alternative: the ultra-precise, 3D-printed miniature. The company’s models — made from a choice of resin, plastic and sandstone-esque material — help architects and their collaborators to communicate their visions. Once a building has been erected, the models also function as compelling displays, drawing the eye much the way a dollhouse would.
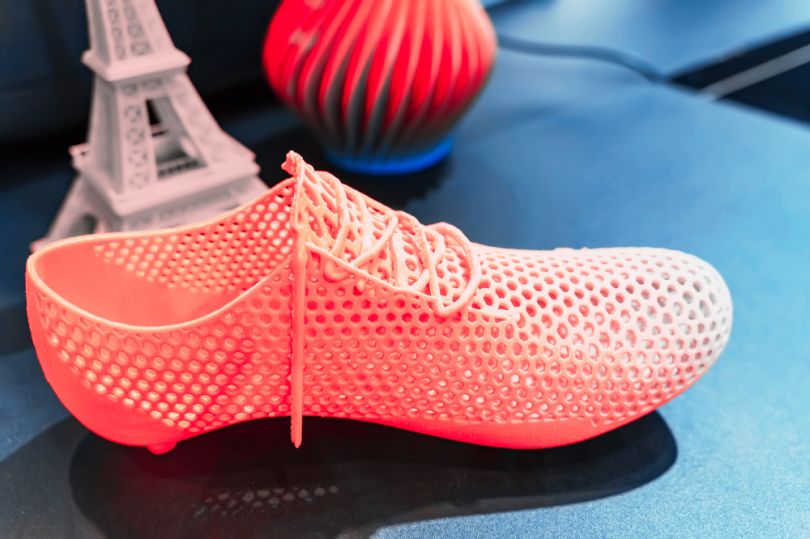
3D Printing in Fashion
Though 3D printers are versatile, they’re not omnipotent. They excel at printing plastic-like materials, but printing anything that drapes or feels good to touch remains prohibitively expensive. That makes cloth a no-go, for now.
Still, cloth is far from the only thing we wear. Plasticky accessories, from sunglasses to footwear, blend right into a modern wardrobe. Some of these are 3D printed — though not Jelly sandals, surprisingly enough. (They’re plastic, but made with injection molding.)
Location: Somerville, Massachusetts
Formlabs creates 3D printing technology for a wide range of industries and applications. For example, the company offers the Form 3+ printer, which can be used in the creation of custom jewelry pieces. The device allows retailers and designers to produce models they can show customers to ensure a piece meets their needs for style and fit, as well as to make masters for reusable jewelry molds.
Location: Tel Aviv-Yafo, Israel
Being the first fashion designer to create a clothing collection using desktop 3D printers, Danit Peleg grew into a company under the same name which sells customized 3D-printed garments. Since 2020, the company has also offered downloadable files for customers to print garments of their choice at any available 3D printer. In collaboration with Nouns, Danit Peleg’s “3D-printed-later” collection was showcased at the 2022 Metaverse Fashion Week.
Location: Fredensborg, Denmark
Monoqool 3D-prints glasses with a simple, minimalist aesthetic. The designs are so streamlined, they don’t even require screws — the hooked metal arms simply latch into the glasses’ lightweight rims, which are printed from polyamide powder. But the simplicity of the final look belies the work that happens behind the scenes. Technicians customize each Monoqool design to the client’s face shape, style and fit preferences.
In 2019, New Balance first turned to 3D printing company Formlabs for an ambitious, slightly nutty project: the reinvention of foam. Specifically, the company wanted to reimagine the foam it used for sneaker midsoles, the layer of the shoe that absorbs the shock of impact. New Balance sought a springier, more durable material.
Formlabs delivered an entirely new substance: Rebound Resin, a liquid that can be printed in intricate lattice work and hardened under a UV light. New Balance used this substance, as opposed to foam, in its TripleCell sneakers, which offer different levels of support across the foot. “It feels more like a resilient trampoline than foam.” Katherine Petrecca, general manager of New Balance’s Innovation Design Studio, told Wired.
As of 2022, New Balance has pushed this idea to also create fully 3D-printed shoes, such as the Tekela V3+ Magia FG soccer cleat set.
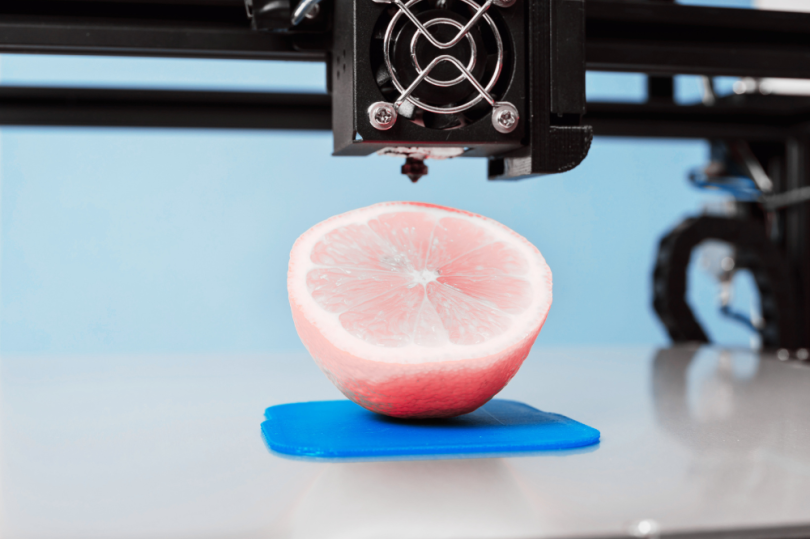
3D Printing in Food
Most 3D printers won’t print just anything — the inner workings were designed to print a particular material, like plastic or metal. Or molten chocolate. Yes, some 3D printers can print food — though typically only if it has a paste-like texture. In fact, an ultra-exclusive pop-up restaurant, Food Ink, serves only 3D-printed dishes: Think desserts arranged in perfect spirals and lobster-shaped seafood dishes.
3D printed food isn’t just for elite dining experiences, either. The technology can shape home cooking too, adding new designs and possibilities into the mix.
Location: Parma, Emilia-Romagna, Italy
In the pasta world, shape is everything. It affects a dish’s mouthfeel, the way it absorbs sauce and its look on a plate. That’s why Barilla hosts an annual contest for the best 3D pasta design. One past winner: Lune, a spherical, crater-pocked design inspired by the moon.
It takes Barilla’s fridge-sized 3D printer between two and three minutes to print nine pieces of pasta from semolina dough, which means the printing process doesn’t run much faster than human artisans. Still, Barilla is deeply invested in its possibilities. In fact, they created a spinoff company, BluRhapsody, that specializes in custom 3D-printed pasta for sale.
Location: Hershey, Pennsylvania
In 2014, Hershey unveiled a 3D printer for chocolate: the CocoJet, created in collaboration with 3D Systems. If it sounds pretty easy to turn a plastic printer into a chocolate printer, think again. The CocoJet required painstaking customization.
“Chocolate has much different melting and cooling properties than something like plastic,” Jeff Mundt, Hershey’s Marketing Manager of Tech, told TechCrunch.
Since it currently takes about 90 minutes to print a full-size Hershey Chocolate Kiss, Hershey’s restricted the printer to 2D use during its displays at Hershey’s Chocolate World in Pennsylvania for the time being.
Location: Baltimore, Maryland
Not a meat eater but still craving a steak? Seeking to commercialize “Meat 2.0”, Mooji Meats is working to manufacture 3D-printed plant-based meats, ranging from chicken to fish. The company is to specialize in creating plant-based whole cuts of meat in both an affordable and environmentally-sustainable manner. Mooji Meats hopes to develop its first prototype of 3D-printed meat within 2022.
Location: Barcelona, Catalonia, Spain
Natural Machines doesn’t make a desktop 3D printer so much as a countertop one. The Foodini, its toaster-oven-sized food printer, allows for custom portion sizes, designs and plating. Home chefs simply program its touch-screen interface, preloaded with suggested shapes, and slot fresh ingredients into the printer’s five capsules. It then produces edible creations like guacamole, geometric cookies — even a butter sculpture in the shape of a human head.
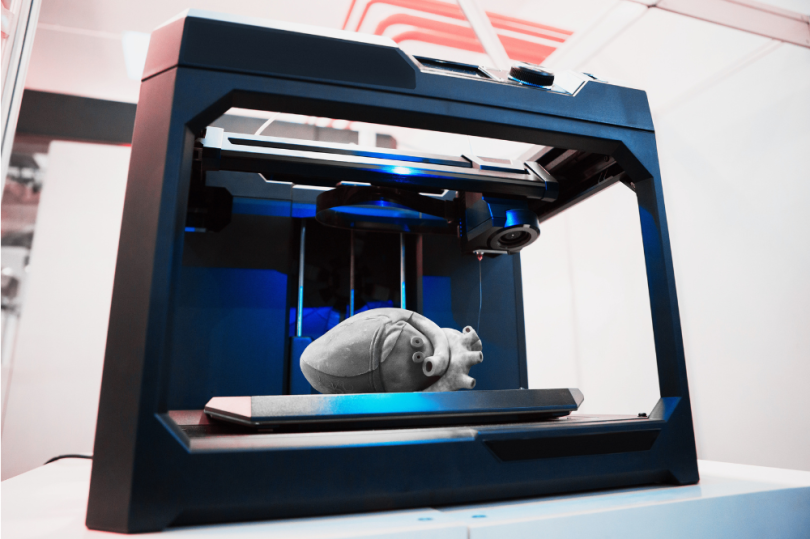
3D Printing in Healthcare
3D printers don’t have a great bedside manner — they look more like futuristic bread boxes than nurses. Still, they can indirectly care for sick and disabled people, printing out artifacts ranging from assistive devices to near-functional human hearts.
Location: Chicago, Illinois
Getting an organ transplant is a terrifying ordeal, often involving a long waitlist and an uncertain future. However, BioLife4D aims to change that by 3D-printing functional human hearts, a process called “bioprinting.”
In 2019, using a gelatin-like ink made from human stem cells, the team successfully printed a functional miniature heart. The ultimate aim is to scale-up, creating a “commercially viable and sustainable” solution for patients. In the meantime of continued research, the team has filed for an Initial Public Offering with the U.S. Securities and Exchange Commission as of 2022.
Location: Burlington, Massachusetts
Securing $50 million in Series C funding in 2021, LightForce creates fully customizable orthodontic bracket systems and placement trays, all from 3D printing. Each set of brackets is made of ceramic polycrystalline aluminum material, and uses a patient’s teeth scans to be printed specifically to their size and anatomy. LightForce has worked with a handful of orthodontic practices across the United States to streamline treatment and offer further braces options for patients.
Location: Leuven, Belgium
Based in the EU, Materialise runs a 3D printing factory with eight printer models capable of working with more than 30 materials — which means it can print almost everything. Some of its most noteworthy creations are custom shoulder and hip implants. The process works like this: Staff engineers review a patient’s CT scans, and craft a design for a titanium implant tailored to that patient’s physiology. To date, Materialise implants have helped patients recover from ailments including arthritis and gunshot wounds.