Work Flexibility: Hybrid
Who we want: ·Collaborative partners. People who build and leverage cross-functional relationships to bring together ideas, data and insights to drive continuous improvements across the business·Data communicators. Highly effective communicators who can transform data findings into recommendations to compose reports and executive level presentations.·Self-directed initiators. People who take ownership of their work and need no prompting to drive productivity, change, and outcomes.·Dedicated achievers. People who thrive in a fast-paced environment and are driven to complete projects that meet regulations and expectations.·Analytical problem solvers. People who go beyond, by identifying root causes, evaluating optimal solutions, and recommending comprehensive solutions to prevent future issues.What you will do:
- Primarily responsible for Risk management, Risk Table creation & Analysis, FMEAs, Quality Plan, Literature Review, Device Master Record, Quality Training Plan and Technical File.
- Product risk assessment as per ISO14971
- Primary participant in new supplier selection, validation, and contract development. Assists vendors in resolving manufacturing and quality issues as required.
- Partners with the operations team to develop and maintain a robust internal and external supply chain.
- Contribution examples include the performance of supplier audits, risk assessment/mitigation, and coaching.
- Develop procedures for incoming, in-process and final inspections for new product development
- Assists/Leads in the trending and analysis of quality data (e.g. complaints, scrap, warranty return rate, etc.) and provides guidance to address issues as appropriate.
- Authors and reviews procedures to ensure GMP and ISO 13485 compliance.
- Lead product quality related projects. Supports the business in addressing and solving quality problems
- Conduct internal audits & participate in corporate and FDA audits
- Support process validation programs for new product development
- Work with cross-functional/cross –cultural teams to develop regulatory guidelines and procedures
- Provide inputs for NPDP for adherence to QMS and Good Documentation practices
- Work with engineering & manufacturing teams to develop robust verification test strategies to ensure product safety and reliability
- Must have delivered multiple projects in AQE function and understand Risk Management processes in depth.
What you need:
- Bachelors in mechanical/biomedical/Biotech Engineering.
- Good analytical and problem-solving skills.
- Good understanding of Quality Management Systems. (ISO 13485, 21 CRF 820)
- 3-5 years of relevant work experience.
- Experience on NPD process and various phases of new product development.
- Knowledge of ISO 14971, IEC 62366, 60601-1 family of standards.
- Demonstrated ability to effectively work with others in various coordinate disciplines and on multi-national teams.
- Expert-level knowledge of current industry standards for New Product Development and risk management practices.
Travel Percentage: 10%
What We Do
Stryker is a global leader in medical technologies and, together with its customers, is driven to make healthcare better. The company offers innovative products and services in MedSurg, Neurotechnology, Orthopaedics and Spine that help improve patient and healthcare outcomes. Alongside its customers around the world, Stryker impacts more than 130 million patients annually. More information is available at www.stryker.com.
Together with our customers, we are driven to make healthcare better.
Gallery
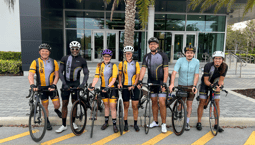