ROLE SUMMARY
Under the supervision of the Automation Supervisor, the Automation Technician will provide technical support to Utilities, Laboratories, and Production Areas in the Automation and Control System Applications used in the manufacture of sterile injectable. The technician will assist in troubleshooting PLC's, batch applications, instrumentation, human machine interfaces, control systems, and process network applications used in utilities, laboratories, manufacturing, and packaging equipment. They will provide technical guidance and assistance to the troubleshooting, operation, and maintenance of control systems including hardware and software. In addition to these responsibilities, the technician will back up their supervisor in the assignment and review of the automation workload. Working as part of a team, the technician will provide technical knowledge and guidance for designated interface groups, and carry out installation, diagnostics, repair, and ensure the reliability of industrial control systems and equipment.
ROLE RESPONSIBILITIES
Troubleshooting:
- Supports the Automation team in tasks that may require collaborative efforts.
- Assists with factory acceptances, software upgrades, backups, restore, disaster recovery, and archiving procedures under supervision.
- Learns to read and interpret ladder logic programming, blueprints, schematics, and specifications to assist in troubleshooting and determining causes of equipment malfunction. Maintains communication with external firms for out-of-plant equipment/system repair.
- Assists in basic troubleshooting of non-functioning components including servos, sensors, PLC, HMI, robotic systems, and control components with guidance.
Technical Support:
- Assists and learns from external contractor's services to ensure that services are provided as required.
- Communicates with the Automation Supervisor for work priorities, assignments, and to report findings.
- Supports the Automation and Control Systems, and Engineering & Maintenance areas in the development of specifications, selection, FAT, installation, commissioning, and computerized system validation process of new utilities, laboratory, and manufacturing equipment procurement, as well as to improve existing applications.
- Participates in the operation and design analysis of plant utilities, laboratories, and/or manufacturing equipment and systems to learn about their operation. May provide technical support to others, when necessary, under supervision.
Electrical:
- Assists in the installation, repair, and maintenance of electrical systems, equipment, and components under supervision.
- Learns to test electrical systems and components for functionality and safety.
- Helps troubleshoot electrical problems under guidance, identifying root causes and supporting corrective actions.
- Participates in routine inspections and preventive maintenance on electrical systems and equipment.
- Assists in replacing or repairing faulty electrical components with supervision.
- Works alongside other trades and contractors on construction projects to learn proper coordination of electrical work.
- Helps maintain accurate records of electrical work performed, under supervision.
- Receives technical support and guidance from more experienced maintenance staff.
- Adheres to safety protocols and procedures to prevent accidents and electrical hazards.
- Supports emergency calls and service requests to address electrical issues under guidance.
Packaging and Serialization:
- Gains knowledge of Serialization terminology and structure in the packaging lines.
- Assists in troubleshooting between the line Master and integrated local equipment under supervision.
- Supports troubleshooting between the line Master and the side Serialization servers (OSM).
- Develops communication and teamwork skills with off-site colleagues/departments managing Serialization servers (BT group).
- Learns to communicate and collaborate with OEM of Serialization system.
- Assists in performing Label Associations in the packaging lines according to SOP approved and artwork.
- Acquires knowledge in camera system operation and maintenance.
Maintenance:
- Assists the Maintenance team with the commissioning, calibration, and adjustment of measurement instrumentation under supervision.
- Supports in replacing, repairing, troubleshooting, or cleaning automation systems with guidance.
- Participates in performing preventive maintenance on automated systems alongside experienced technicians.
Automation:
- Learns to modify PLC, HMI, SCADA hardware and configure software in the system to maintain the interface between automation and operations with oversight.
- Assists in reading and interpreting ladder logic programming, blueprints, schematics, and specifications to support troubleshooting efforts. Maintains communication with external firms for out-of-plant equipment/system repair under supervision.
Network Maintenance and System Administration:
- Supports the maintenance of industrial-level networks, control level networks, and Process I/O network under the guidance of a senior technician.
- Assists in managing user access to the Site Automation system, ensuring that all actions are supervised and authorized.
- Helps ensure that various user levels have appropriate, documented training and authorization for access to engineering managed computer systems, under the direction of a system administrator.
Reliability Engineering:
- Provides support for reliability engineering tasks related to production and support equipment under the guidance of experienced engineers.
- Offers operational support on the floor as needed, under supervision.
- Assists in investigations and audits as required, ensuring compliance and support for the maintenance team.
Laboratory Systems:
- Supports the application administrator on all computerized systems with oversight.
- Assists the system administrator for legacy computerized systems not on the network.
- Participates in auditing instruments capable of being audited.
- Helps with backup/archive systems as required.
- Assists in performing user access requests and reviews under supervision.
- Supports the validation of systems in the system administrator role.
- Aids in troubleshooting application/instrument issues with guidance.
- Learns to calibrate systems through applications and perform system health checks.
- Ensures all non-networked equipment time remains within tolerance to the network clock, under supervision.
- Assists in maintaining the security of limited security systems.
Facilities and Utilities Systems:
- Develops knowledge and understanding of the Utilities Monitoring System (UMS).
- Learns about the Water for Injection (WFI) systems and loops.
- Gains knowledge in flow meters, level devices, and valves.
- Acquires an understanding of the Reverse Osmosis (RO) and Purified water systems.
- Builds knowledge and understanding of the Building Maintenance System (BMS).
- Learns about overhead alarms, Air Handling Units, and Cold rooms.
- Receives training in VFD set-up and programming.
Additional Responsibilities:
- Facilitates communication between staff engineers, external technical representatives, operations, and maintenance personnel under supervision.
- Gains experience with control system maintenance and supports associated project development/implementation.
- Assists with the installation, diagnostics, repair, and reliability of industrial control equipment (e.g., instrumentation, industrial communications, DCS, HMI, PLC, PC interface, and third-party equipment) under guidance.
- Actively participates in safety and environmental programs and other programs as determined by management.
- Helps repair, modify, and install computer software, hardware, and peripheral devices related to legacy/current PCs.
- Provides technical support and assistance to system users, when necessary, under supervision.
- Assists in maintaining connectivity for legacy systems.
- Supports regular tests, upgrades, and backups.
- Keeps up with required site trainings.
- Assists in making prioritization decisions based on production requirements, in alignment with Supervisor guidelines.
Basic Qualifications:
Minimum Qualifications:
- High School Diploma or Equivalent
- Able to work with diverse teams and focus on inclusion.
- Experience in a production environment, particularly as it relates to automation technology.
- Some programming knowledge and experience with computer programming and software development.
- Basic electrical/electronic troubleshooting knowledge.
- The selected candidate shall demonstrate the ability to apply knowledge and skills.
- Ability to troubleshoot equipment and perform complex system tests.
- Problem-solving skills and analytical skills.
- Organizational skills and attention to detail.
- Creative thinking skills.
- Moderate verbal and written communication skills.
- Ability to communicate well with other members of the development team.
- Ability to keep up with the latest technologies.
- Ability to work weekends, holidays, rotating shifts, and both scheduled and unscheduled overtime as business needs dictate.
Preferred Qualifications:
- Associate degree in a related field with 1 year of experience equivalent to a pharmaceutical control system application, instrumentation, or systems/equipment technician is required.
- 1 year experience or basic knowledge in SCADA, HMI/PLC, or DCS based control systems.
- 5 years of experience in a related field equivalent to a pharmaceutical control system application, instrumentation, or systems/equipment technician is required.
- English proficiency.
- Computer Literate.
- Experience & Skills:
- Knowledge of cGMP, FDA, and other countries' regulatory agencies.
- Knowledge in Computerized Maintenance Management Systems (e.g., preventative maintenance, work orders).
- Must be able to use tools and equipment including electronic testers, oscilloscopes, programmers, and meters to test instruments, equipment, and electronic controls.
- Experience with PLC's based systems, SCADA, and network applications. Must have knowledge of instrumentation and control systems to troubleshoot malfunctions.
- Able to understand and work with computerized maintenance management systems such as spare parts, preventive maintenance, and work orders.
- Electrical controls troubleshooting experience.
- Technical knowledge of utilities equipment (i.e., HVAC equipment, AHU's, VAV's, boilers, chillers, etc.) and production equipment (aseptic filling machine, autoclave, freeze dryers, packaging lines, etc.)
- Must have blueprint and electrical, controls, schematic/ladder logic comprehension skills.
- The physical demands described are representative of those that must be met by an employee to successfully perform the functions of this job. Reasonable accommodations may be made to enable individuals with disabilities to perform the essential functions.
- Must be able to safely perform the job without posing a direct threat to the safety of his or her own self, or the safety of others.
- Ideal candidate will have process automation experience with integrated manufacturing systems and ancillary equipment.
- Familiarity with industrial communication networks.
PHYSICAL/MENTAL REQUIREMENTS
• To perform all the duties required in this job description, persons must be in a physical condition that is able to work on ladders and other equipment in less than desirable areas (i.e., mechanical rooms).
• Ability to work in gown room conditions.
• Light to moderate lifting may be required for some duties. Must be able to lift 50+ pounds.
• Proper Personal Protective Equipment (PPE) and safe practices must be observed.
• Requires continuous physical activity for repair, adjustment, and troubleshooting of equipment/systems.
• Some areas present exposure to heat, steam, and liquids.
• Satisfactory performance and attendance are required.
• Ability to understand and apply verbal and written work and safety-related instructions and procedures given in English.
• Must be able to work in a potentially stressful environment.
• Work is performed in a pharmaceutical plant which may include exposure to moving mechanical parts, risk of electrical shock, laboratory settings, and clean room environment.
• Ability to follow regulatory guidelines.
• While performing the duties of this job, the employee is required to stand, sit, demonstrate manual dexterity, climb stairs and ladders, work on elevated platforms, and tight and enclosed spaces.
• Work is on-site with limited remote work and travel.
NON-STANDARD WORK SCHEDULE, TRAVEL OR ENVIRONMENT REQUIREMENTS
Regular Work Schedule:
• Day shift (start time 0600). 12 hour schedule. Overtime work may be required. Work requires on-site presence. Occasional national/international travel for equipment factory acceptance testing, training seminars, vendor meetings, work progress meetings, etc
Non-Regular Work Schedule:
• At different times of the year, this position will work long hours for scheduled manufacturing shutdown periods and throughout the year may be required to work late with little notice as need arises when equipment is unexpectedly down.
Colleague may be asked to work weekends, holidays, and on various shifts and schedules dependent on business need.
Work Location Assignment: On Premise
The salary for this position ranges from $28,19 to $46,99 per hour. In addition, this position offers eligibility for overtime, weekend, holiday and other pay premiums depending on the work schedule and the Company's policies. We offer comprehensive and generous benefits and programs to help our colleagues lead healthy lives and to support each of life's moments. Benefits offered include a 401(k) plan with Pfizer Matching Contributions and an additional Pfizer Retirement Savings Contribution, paid vacation, holiday and personal days, paid caregiver/parental and medical leave, and health benefits to include medical, prescription drug, dental and vision coverage. Learn more at Pfizer Candidate Site - U.S. Benefits | (uscandidates.mypfizerbenefits.com). Pfizer compensation structures and benefit packages are aligned based on the location of hire. The United States salary range provided applies only to the United States - Kansas - Mcpherson location.
Relocation assistance may be available based on business needs and/or eligibility.
Sunshine Act
Pfizer reports payments and other transfers of value to health care providers as required by federal and state transparency laws and implementing regulations. These laws and regulations require Pfizer to provide government agencies with information such as a health care provider's name, address and the type of payments or other value received, generally for public disclosure. Subject to further legal review and statutory or regulatory clarification, which Pfizer intends to pursue, reimbursement of recruiting expenses for licensed physicians may constitute a reportable transfer of value under the federal transparency law commonly known as the Sunshine Act. Therefore, if you are a licensed physician who incurs recruiting expenses as a result of interviewing with Pfizer that we pay or reimburse, your name, address and the amount of payments made currently will be reported to the government. If you have questions regarding this matter, please do not hesitate to contact your Talent Acquisition representative.
EEO & Employment Eligibility
Pfizer is committed to equal opportunity in the terms and conditions of employment for all employees and job applicants without regard to race, color, religion, sex, sexual orientation, age, gender identity or gender expression, national origin, disability or veteran status. Pfizer also complies with all applicable national, state and local laws governing nondiscrimination in employment as well as work authorization and employment eligibility verification requirements of the Immigration and Nationality Act and IRCA. Pfizer is an E-Verify employer. This position requires permanent work authorization in the United States.
Engineering
#LI-PFE
Top Skills
What We Do
Our purpose ensures that patients remain at the center of all we do. We live our purpose by sourcing the best science in the world; partnering with others in the healthcare system to improve access to our medicines; using digital technologies to enhance our drug discovery and development, as well as patient outcomes; and leading the conversation to advocate for pro-innovation/pro-patient policies.
Why Work With Us
We are the inventors, the problem solvers, the big thinkers — those who surmount any hurdle to deliver breakthrough medicines to the people who are counting on them the most.
Gallery



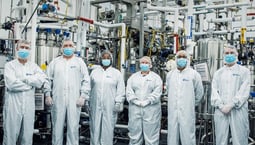

Pfizer Offices
Hybrid Workspace
Employees engage in a combination of remote and on-site work.