When Jacob Haip walks into Formlabs, he sees the physical emblems of each of his co-workers’ personal lives. The full stack web engineer might encounter a brand new video game character, niche robots or complex 3D models on display — even custom chess sets catch the eye. Inside the office, almost anything is possible.
“It’s really fun and spontaneous working in 3D printing, because one of the perks of working here is being able to use our printers to print whatever we want,” Haip said. “I love walking around the office and seeing all the cool things people print related to their hobbies.”
Like its employees’ interests, Formlabs is in the business of creation without limitations. With a company motto of “anyone can make anything,” approachability and accessibility are consistent points of conversation when embarking on any new project — especially in an industry that requires forward thinking to fill unprecedented demands. From jewelry and home improvement tools to biomedical prosthetics, it can be done.
When Materials Scientist Olivia Damore began working with biocompatible resins in Formlabs’ new dental business unit, she wasn’t sure of her role in the 3D printing process. With a biology degree and no previous engineering experience, she was suddenly on a team dedicated to developing and launching Formlabs’ first biocompatible material that was both FDA approved and could be safely used in dental patients’ mouths. After extensive verification and validation — as well as obtaining the ISO certification — the Surgical Guide resin was a success.
THE INTERNATIONAL POSSIBILITIES OF 3D PRINTING
“Formlabs is made of people from all backgrounds and experiences and is open to what you can bring to the table, even if it’s not something that seems obvious to the industry,” Damore said. “I’m not a materials scientist by training, but my degree and previous work experience provides me with unique perspectives that I can offer to the team. We really appreciate a multi-faceted approach at Formlabs, as it’s what allows us to put the best products possible into the hands of our customers.”
That belief that any background has a place at the company carries over into the work employees do every day for their clients, customers and beyond. According to Mechanical Engineer Jake Sanchez, it’s that same approach that pushes Formlabs to always be at the cutting edge of what’s possible and continue breaking boundaries.
“I think you could point to the whole of Form 3 — Form 3 is a groundbreaking machine. It works like no other 3D printer on the market,” Sanchez said. “We developed our own light processing unit, a novel line-scanning machine architecture and a unique flexible resin tank; that was a ground-up rethink of how to do 3D printing in the SLA space. I think if a company our size pitched that idea to the industry at large back when we started development it would have seemed more than ambitious — but we managed to pull it off with our technology-first development process and dynamic engineering team.”
Built In connected with Haip, Damore and Sanchez to learn more about how Formlabs is reshaping the future of what’s possible through 3D printing. Damore summarized it best: “You’ll gain just so much life knowledge at Formlabs — not just the skills needed to be a better engineer or scientist, but real life translatable skills that can only come from working in such a customer-focused innovative space like Formlabs.”
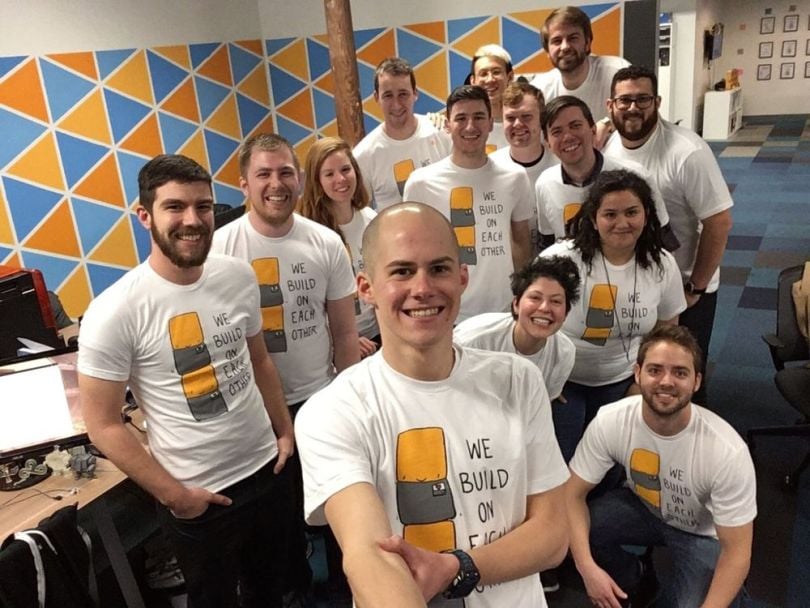
What stands out most to you about the culture at Formlabs? What opportunities do employees have to shape that culture?
Olivia Damore: It’s not only super collaborative and helpful on the materials team, but also full of really passionate scientists and problem solvers. I think a lot of labs and companies can be on the competitive side, but Formlabs has felt nothing but supportive. A lot of teams at Formlabs are small enough that you feel that sense of camaraderie, but have enough people from a variety of backgrounds that you’ll always find someone who is an expert in any topic. Anytime that I have a question or need help, I can find someone willing to sit down and brainstorm with me.
Jake Sanchez: I think a big thing that comes into Formlabs’ work culture — particularly the hardware side — is that we talk a lot about ownership and autonomy.
WHAT IS A FORM 3 MACHINE?
If you look at a lot of other companies that offer machine or mechanical design, you may be working from a playbook that is as old as time itself — doing some very upstream design work that then gets pushed off to somebody else to implement, and it disappears down the chain. But here at Formlabs, we are so hands-on with every step of the process. You will design, build and test prototypes, and feel a sense of ownership and responsibility for this thing you’re creating. We’re not designing in an ivory tower — we’re right there in the thick of it from the R&D labs to the assembly lines.
We experience these dynamics daily because we’re inherently collaborative. We build multidisciplinary things because our printers are electromechanical and optical and chemical, and all these different disciplines have to meld. 3D printers are still relatively new so there’s not a ton of precedent as far as what it is that we’re building and how we’re building it.
What are some of your current hiring goals or challenges for your department teams? Why should any seasoned engineering job seeker be paying attention?
Jake Sanchez: If you told me that we could double our number of hardware engineers and technicians, I would have work for every single one of them. We aren’t content with just our current hardware portfolio but are looking to continuously improve and expand the digital fabrication capabilities offered by Formlabs products. In order to fuel this we’re looking for hardware design and manufacture specialists to form the cornerstone of these new engineering efforts.
Olivia Damore: We’re always hiring people to help support our efforts. Because we are a growing company, there are now so many different facets to Formlabs. On and adjacent to the materials team alone, we have people working on R&D in powders and resins for a variety of industries, we have roles in regulatory affairs, dental professionals, and print process engineers just to name a few. Right now I’m looking for a technician to help me in our brand new cell culture room at our HQ office, which allows us to test the cytotoxicity of our materials that we’re developing. I haven’t seen many applicants with a bio background because maybe someone with a biology degree doesn’t think they have a place at a 3D printing company. I would encourage any applicant to think outside of the box in their search.
“One of the coolest things about Formlabs is that we really could use somebody from every background.”
Jacob Haip: On the software side, we’re hiring for every part of the software stack. One of the most exciting parts about software at Formlabs is that what you’re making isn’t just an app or something on a flat, 2D screen. It’s the most tangible, exciting experience in your everyday work where you can actually hold the things you work on. It’s the reason I’ve stayed at Formlabs for so long.
What tools are essential within your individual tech stacks to continuously innovate your products at Formlabs? How do you constantly stay ahead of the curve?
Jacob Haip: The challenge from the software team is to not only make the printer hardware work, but also make it print better every month as we release updates and new materials. For example, new support structures that make printed parts more accurate and easier to remove — these are all things we can make possible through software.
Olivia Damore: To make the most cutting-edge materials, I would say the most valuable tool is our relationships. Formlabs is a very empathetic, customer-driven company in that we want to make it easier for our customers to have the best materials and printers possible to solve real world problems. We have an amazing product team that has formed relationships with many invaluable industry professionals that provide us first hand insight and feedback on what the customer is looking for. We don’t stop formulating until we get it right. Our ethics at Formlabs have allowed us to foster creative relationships with our raw materials suppliers — they are always eager to come onsite to offer guidance on which products they can offer or help us create to make the best resins for our customers. As scientists, we are constantly problem solving and learning and we rely heavily on teamwork both internally and externally.
To make the most cutting-edge materials, I would say the most valuable tool is our relationships.”
Jake Sanchez: Since I work in mechanical engineering, I’ve got to talk about computer-aided design (CAD). We use Onshape here at Formlabs. I never thought I’d say this, but it’s really great to be cloud-based. I can take my laptop home and have just as much modeling power as when I’m here in the office, I can zip into a model and look at what other people on my team are working on, and I can easily share designs with other teams for meetings — it’s just huge for collaboration.
Also, I really take for granted how easy 3D printing is here! I once bootstrapped a project by printing 80 percent of an SLA printer prototype in-house on a Fuse 1 and it was incredible. It’s so freeing and powerful to be able to draw up a prototype in CAD, place an order for hardware, and then throw the rest of the design to our fleet of printers so I can assemble by lunchtime the following day. You can’t get that in a place that doesn’t have 3D printing capabilities like we do.
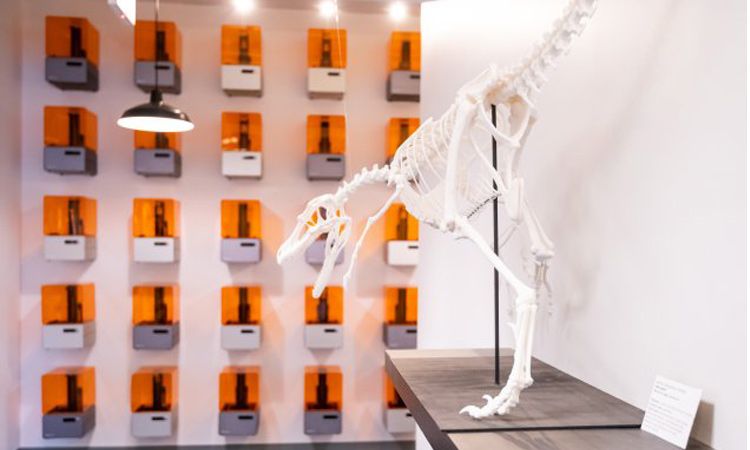
How have you grown personally and professionally during your time at Formlabs, with more than four years experience for each of you?
Jake Sanchez: When I first joined, I was new to 3D printing and saw the Form 3L team go from five people to 100 people as the project gained momentum heading towards launch. I learned a ton, and from some of the best people I’ve ever had the pleasure of working with. Now I’m a Senior Mechanical Engineer on the SLA team trying to find the best way to translate the experience and skills that I’ve gained to help everyone reach their potential. I think the great thing about Formlabs is you can’t ever stop learning while working here. It’s that sense of fun that’s kept me around.
Jacob Haip: I started as an intern at Formlabs in my junior year at MIT. Back then, Formlabs only made the Form 1+ printer and we had no web-connected printers and remote monitoring management didn’t exist yet. After I graduated, I got a return offer here at Formlabs around the launch of the Form 2 printer, which was our first Internet-connected printer and the first time we could offer remote control and management. Over the years, team sizes have grown, and I’ve transitioned to the tech lead position. It’s been great to continuously grow along with Formlabs, but we’re still a small, tight-knit group.
Olivia Damore: I think it’s been really rewarding to experience personal growth alongside the growth of the company over the past 4 years. When I first started here, I was a technician fresh out of college trying to find my place as a biologist on a team of materials scientists. While Formlabs was growing at a pace that felt tangible and exciting, I didn’t quite realize how much I would grow as a person and scientist. I knew that I wanted to work on the biocompatible side of the materials team and my managers collaborated with me to put me on projects I was passionate about. Since then, I transitioned from technician to scientist, and the materials team has gone from a handful of scientists — and the lab a handful of square feet — to a brand-new, state-of-the-art lab full of innovators. Formlabs has expanded in locations, hardware, number of employees, business units and evaluations. Despite its growing size, everything here remains very hands-on and personal. That hands-on experience is what grows you as a professional and what makes Formlabs the company that it is.