Job Number: 69209
Group: Magna Powertrain
Division: Sterling Heights
Job Type: Permanent/Regular
Location: STERLING HEIGHTS
Group Introduction
Advancing mobility. Making automotive technology that is smarter, cleaner, and safer, while still fun to drive. And making it for everyone. That's what we're passionate about at Magna Powertrain. We do it by creating world-class powertrain solutions for conventional, hybrid, and pure electric vehicles. We're making electrification more than a buzzword, we're bringing it to the road. Innovation is what drives us and we drive innovation. Dream big and create the future of mobility at Magna Powertrain.
Objective & Scope
The Die Setter is responsible for setting dies in presses in a safe and effective manner. All aspects and functions of the work required to change a specific machine, resource or die from making the last good piece of the current job to the first good piece of the next job in a timely manner and assuring all paperwork is correct.
Responsibilities, Duties and Authority
- Locate die, associated tooling & gauging and proper material for job set up.
- Responsible for continuously improving the process or changeover to reduce the time it takes for changeovers.
- Keep die racks and finger bar racks neat, clean and organized.
- All chutes and miscellaneous die set equipment must be properly put away.
- Operate hi-lo, crane and any other equipment required to transfer equipment.
- Ability to transfer the die in the proper manner.
- Align the die, steel, feeder, etc., and secure the equipment as required.
- Adjust press, feed, coil height, knockout, air pins, as required to obtain inspection approval and safe operation.
- Set up Peripheral equipment such as guards, conveyors, lubricators, and unloading devices.
- Perform related labor as required to clean up, set up, and organize. Return the dies and materials to the proper location.
- Cut off or make air pins, parallels, knockouts, chutes etc. as required.
- Maintain and record all related paperwork such as die set up sheets, checklists etc.
- Perform first off inspections with established inspection methods to confirm setup / changeover was performed correctly.
- Must be able to run 200 pcs before releasing job to the operator.
- Provide training to Press Operator I's.
- Participate in internal, external and LPA audit activities when required.
- Instruct Press Operator I's during die changes to assist in die set.
- Assist with coordination of production floor including MAFACT activities, training of employees and driving best practices.
- Ensure that company policies and procedures are adhered to including IATF 2016:16949, ISO14001 (EMS), Mafact and Employee Handbook.
- Follows MIOSHA and MPTSH safety regulations and policies, including wearing required P.P.E. (Personal Protective Equipment) and Lockout. Reports unsafe conditions to Supervisor/Leader.
- Complies with the designated ISO / 14001 responsibilities related to effective environmental management in accordance with MPT's Environmental Management System (EMS).
Education and/or Experience:
High School Diploma or GED. 2-3 years of die setting experience with metal stamping dies, including progressive, transfer and line dies. At least 2-3 years' experience adjusting and programming transfer systems. Ability to perform heavy manual labor such as bolting dies into presses. Knowledge of MIOSHA standards. Able to work independently. Ability to work with others in a fast paced team environment. Ability to exercise initiative, common sense and ability to maintain effective internal and external working relationships. Results-oriented team player. Highly organized, self-starter with a positive attitude. Flexibility to work extra hours when needed and different shifts. Excellent attendance and performance record. Self-starter with a positive attitude. Must have own tools.
Additional Skills
Language Skills: Ability to read and comprehend instructions in English and correspondence such as safety rules and operating instructions. Ability to document forms as required by position. Able to communicate in English effectively, (read and write). Strong communication (oral and written) skills.
Mathematical Skills: Ability to add, subtract, multiply and divide in all units of measure, using whole numbers, common fractions and decimals. Ability to compute rate, ratio and percent.
Computer Skills: To perform this job successfully, an individual should have knowledge of AS400 and ability to use bar code labeling system. Experience with Microsoft Office (Word, Excel, Outlook) preferred.
Reasoning Skills: Ability to apply common sense understanding to carry out instructions furnished in written, oral, diagram, or schedule form. Ability to deal with problems involving several concrete variables in standardized situations.
Communication Skills: Ability to use active listening and assertive communication when needed. Ability to give positive and negative feedback effectively. Treat co-workers with dignity and respect and in accordance with the Magna Employee's Charter and Common Values.
Awareness. Unity. Empowerment.
At Magna, we believe that a diverse workforce is critical to our success. That's why we are proud to be an equal opportunity employer. We hire on the basis of experience and qualifications, and in consideration of job requirements, regardless of, in particular, color, ancestry, religion, gender, origin, sexual orientation, age, citizenship, marital status, disability or gender identity. Magna takes the privacy of your personal information seriously. We discourage you from sending applications via email to comply with GDPR requirements and your local Data Privacy Law.
Nearest Major Market: Detroit
What We Do
We are a mobility company that innovates like a start-up and thinks like a technology company. This helps us anticipate change in one of the most complex industries in the world and respond quickly. We depend on a team of 171,000 dynamic, entrepreneurial-minded employees in an environment where great ideas flourish. Our presence spans 343 manufacturing operations and 88 product development, engineering and sales centers in 29 countries.
We understand that you need a career as unique as you are. Whether you want to advance your existing expertise or try something completely different, we are committed to your growth.
Why Work With Us
At Magna, our engineering team is advancing mobility for everyone and everything. Joining this team means being a part of the design, development, and manufacturing of the world’s most advanced mobility technology. Innovations that move families, shape communities, and improve lives. You can follow your passions and shape your own career path.
Gallery
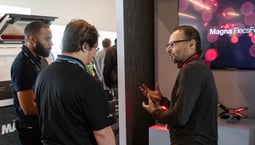
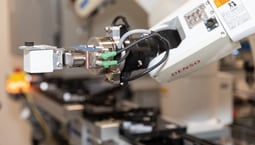
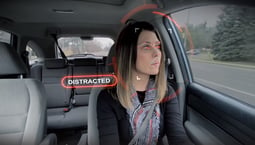
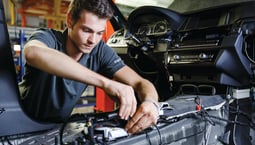
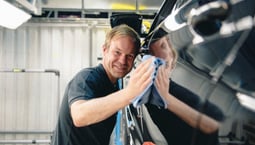
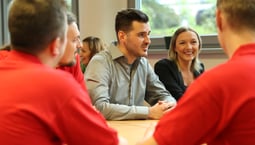
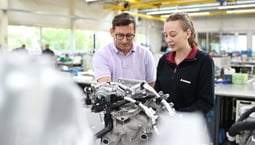
Magna International Teams
Magna International Offices
Hybrid Workspace
Employees engage in a combination of remote and on-site work.
Majority of roles are hybrid with flexibility. Please speak with our recruiting team for specific details on hybrid work.