What we offer:
At Magna, you can expect an engaging and dynamic environment where you can help to develop industry-leading automotive technologies. We invest in our employees, providing them with the support and resources they need to succeed. As a member of our global team, you can expect exciting, varied responsibilities as well as a wide range of development prospects. Because we believe that your career path should be as unique as you are.
Group Summary:
Transforming mobility. Making automotive technology that is smarter, cleaner, safer and lighter. That's what we're passionate about at Magna Powertrain, and we do it by creating world-class powertrain systems. We are a premier supplier for the global automotive industry with full capabilities in design, development, testing and manufacturing of complex powertrain systems. Our name stands for quality, environmental consciousness, and safety. Innovation is what drives us and we drive innovation. Dream big and create the future of mobility at Magna Powertrain.
Job Responsibilities:
The Materials System Specialist is responsible for ensuring seamless management and coordination of materials, production planning, master scheduling, and steel reconciliation within the organization. This role requires advanced knowledge of SAP MM (Materials Management), SAP PP (Production Planning), and strong analytical skills to maintain accurate inventory levels, optimize production efficiency, and ensure raw material (steel) reconciliation accuracy.
The ideal candidate will work closely with the Supply Chain, Production, Procurement, and Finance teams to ensure production plans are aligned with material availability while optimizing costs and minimizing waste.
KEY RESPONSIBILITIES
- Configure, manage, and maintain the SAP MM module to ensure the seamless flow of raw materials and components into the production line.
- Monitor and manage raw material inventory levels, ensuring stock availability while minimizing excess inventory.
- Facilitate and resolve material shortages, overages, and obsolescence issues.
- Ensure accuracy of Goods Receipt (GR), Goods Issue (GI), and Purchase Order (PO) processes.
- Collaborate with the Procurement team to ensure timely material delivery from suppliers.
- Analyze and reconcile Material Variance Reports (MVR) and investigate discrepancies. Actively and positively support the continued practice of Core Values behaviours and Employee Charter.
- Design, configure, and maintain SAP PP Master Data including Bill of Materials (BOM), Work Centers, and Routings.
- Develop and manage production schedules based on demand forecasts, capacity planning, and raw material availability.
- Monitor planned vs actual production output and adjust schedules as needed.
- Generate Production Orders, Planned Orders, and Capacity Plans in SAP.
- Work closely with the production team to minimize machine downtime and bottlenecks.
- Ensure alignment between Material Requirements Planning (MRP) and Production Schedules. Develop and manage the Master Production Schedule (MPS) in SAP PP.
- Balance production output with demand forecasts and available materials.
- Monitor and maintain optimal stock levels by analyzing Days of Inventory (DOI) and safety stock.
- Optimize production sequences to minimize changeovers and maximize production efficiency.
- Facilitate weekly and monthly Production Planning Meetings with production, sales, and supply chain teams.
- Report on capacity utilization, production yield, and efficiency metrics.
- Drive improvements in Lead Time Reduction, On-Time Delivery (OTD), and Material Availability.
- Manage and control steel inventory (coils, sheets, bars, etc.) in SAP MM.
- Implement and manage a Steel Reconciliation Process to ensure accurate consumption tracking.
- Reconcile Raw Material Issuance vs. Actual Steel Usage.
- Analyze steel consumption variance and investigate discrepancies.
- Provide accurate monthly steel consumption reports to finance and operations.
- Work with suppliers to minimize excess steel orders and reduce scrap levels.
- Ensure all steel material consumption is correctly captured in Production Orders and Goods Issues.
- Optimize yield utilization to minimize steel scrap generation. Create and maintain customized SAP reports for:
- Material Stock Levels
- Production Orders Status
- Material Variances
- Steel Consumption Reports
- Implement and adhere to Mafact initiatives such as Standardized Work and 5S.
- Maintain and develop the necessary work instructions pertaining to the Materials area under the IATF 16949 requirements and train staff accordingly.
- Participate as required in all C-TPAT activities.
- Work in a cost-effective manner and maintains a high standard of quality and excellent workmanship.
- Comply with the applicable responsibilities related to effective quality management in accordance with Magna Global Quality System (MQS) and IATF16949.
- Perform other duties as may be assigned by the Materials Manager.
ENVIRONMENTAL, HEALTH & SAFETY RESPONSIBILITIES
- Lead by example by following Unimotion-Gear's Environmental, Health and Safety policies and procedures.
- Work in compliance with the provisions of the Occupational Health and Safety Act and its regulations, specifically S. 25 and S. 26, Industrial Establishments regulation 851, WHMIS regulation 860, First Aid regulation 1101, and all legal and other requirements that Unimotion-Gear subscribes to, which will include but not limited to, CSA standards, ANSI standards, Ministry of Labour guidelines, and WSIB operating procedures.
- Follow the guidelines and rules as set out by the Employee Handbook and Unimotion-Gear policies and procedures.
- Ensure all licensed employees adhere to CSA B-334-04 Safety Standard for Lift Trucks and that all staff are competent as defined under OHSA.
- Ensure all pre-use and pre-shift inspections are complete and follow up on noted deficiencies to ensure closure.
- In the event of a spill, responsible to conduct a spill investigation and complete a Spill Response Report. Actively participate in Pre-Start Health and Safety Reviews as required by Section 7 of the OHSA.
- Conduct health and safety inspections of Unimotion-Gear facility, both planned and unplanned and supports all plant EMS / OHSAS initiatives & requirements.
- Stop any contractor from acting in an inappropriate manner and ensure all contractors / visitors have appropriate contractor / visitor tag.
- Ensure all employees with licensed skills have current and applicable training and valid licenses/permits.
- Ensure department evacuates the building immediately once fire alarm sounds and ensure all direct reports are accounted for and remain in the assembly area during an emergency evacuation.
- Ensure Environmental, Health and Safety Committee Members are given full support and authority to perform workplace inspections, attend meetings and perform other duties as may be required.
- Ensure all workplace accidents, injuries and / or occupational illnesses are reported immediately, and medical assistance is provided as soon as possible.
- Ensure that all critical accident scenes are not disturbed and are reported to the appropriate authorities forthwith.
- Ensure any reports of unsafe acts / conditions are investigated immediately and corrected forthwith.
- Ensure that the Magna Powertrain Inc. (Corporate) Health and Safety Manager is advised of all Ministry of Labour (MOL) visits, environmental compliance visits (MOE), critical injuries, and work refusals.
- Adhere to all policies and procedures related to C-TPAT (Customs Trade Partnership Against Terrorism)
- Comply with the designated responsibilities related to effective environmental management in accordance with Unimotion-Gear's Environmental Management System (EMS) ISO 14001 and Safety Management System, ISO 45001.
- Expected requirements based on ISO 14001/ISO 45001:
- To ensure that this procedure is communicated and followed by all persons working for or on behalf of the plant.
- To identify the environmental aspects of department activities, products and services in accordance with this procedure.
- Provide leadership, support, and commitment to ensure the effectiveness of the EHSMS (ISO14001-2015/ISO 45001-2018) and it achieves its intended outcomes and is compatible with the strategic direction of the company.
- Communicate the importance of an effective EHSMS (ISO14001-2015/ISO 45001-2018) and conforming to the requirements to the employees and any personnel working for or on behalf the plant.
- Review environmental aspects, risk assessments and risks and opportunities annually.
- To report any changes to their process/products or environmental aspects
QUALIFICATIONS
- 5+ years of experience working with SAP MM, SAP PP, and Master Scheduling.
- Experience with SAP S/4HANA or SAP BI/BO reporting.
- Strong background in lean manufacturing, material yield optimization, and scrap reduction.
- Knowledge of logistics, warehousing, and transportation planning.
- Proven experience in Steel Reconciliation and Material Variance Analysis.
- Strong understanding of Bill of Materials (BOM), Routings, Work Centers, and Capacity Planning.
- Experience in managing Production Orders, Goods Issues, and Goods Receipts.
- Knowledge of MRP, MPS, and Capacity Planning processes.
- Strong analytical skills to reconcile material consumption vs. production output.
- Excellent problem-solving and communication skills.
- Advanced knowledge of Microsoft Excel, Pivot Tables, and SAP Reporting Tools. CTPAT & TISAX knowledge
- Familiar with IATF16949 and ISO 14001 / ISO45001 Quality, Environmental and Safety Management systems
- Must be very detail oriented.
- Must be highly motivated and drive change and continuous improvement.
- A valid Fork-lift truck operating license preferred, but not necessary.
Awareness, Unity, Empowerment:
At Magna, we believe that a diverse workforce is critical to our success. That's why we are proud to be an equal opportunity employer. We hire on the basis of experience and qualifications, and in consideration of job requirements, regardless of, in particular, color, ancestry, religion, gender, origin, sexual orientation, age, citizenship, marital status, disability or gender identity. Magna takes the privacy of your personal information seriously. We discourage you from sending applications via email to comply with GDPR requirements and your local Data Privacy Law.
Worker Type:
Fixed Term (Fixed Term)
Group:
Magna Powertrain
Top Skills
What We Do
We are a mobility company that innovates like a start-up and thinks like a technology company. This helps us anticipate change in one of the most complex industries in the world and respond quickly. We depend on a team of 171,000 dynamic, entrepreneurial-minded employees in an environment where great ideas flourish. Our presence spans 343 manufacturing operations and 88 product development, engineering and sales centers in 29 countries.
We understand that you need a career as unique as you are. Whether you want to advance your existing expertise or try something completely different, we are committed to your growth.
Why Work With Us
At Magna, our engineering team is advancing mobility for everyone and everything. Joining this team means being a part of the design, development, and manufacturing of the world’s most advanced mobility technology. Innovations that move families, shape communities, and improve lives. You can follow your passions and shape your own career path.
Gallery
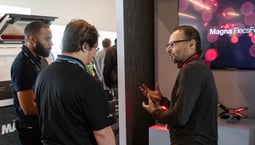
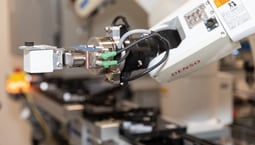
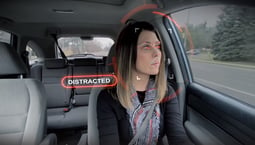
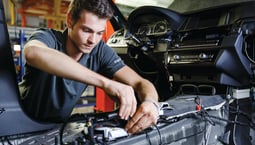
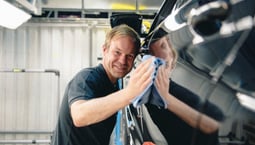
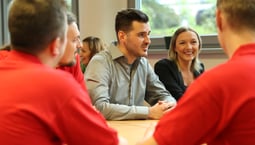
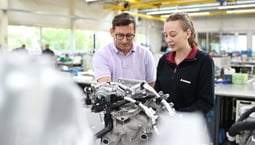
Magna International Teams
Magna International Offices
Hybrid Workspace
Employees engage in a combination of remote and on-site work.
Majority of roles are hybrid with flexibility. Please speak with our recruiting team for specific details on hybrid work.