Heavy-duty trucks are an everyday sight for drivers on the highway, but here’s a reality that might shock you: 35 percent of the time, the trailers of those trucks are empty. “Deadhead miles,” also referred to as “empty” or “non-revenue” miles, accumulate as drivers return home without a load after making a delivery — sometimes over short distances, other times cross-country.
Consuming fuel, emitting carbon, and incurring costs for drivers without earning them billable income, deadhead miles are viewed by the freight industry as a primary form of waste. Consider as well the environmental cost: a reported 61 billion out of 175 billion trucking miles in the U.S. are driven empty, which results in 87 million metric tons of CO2 emissions each year.
Despite its massive scale, the $800-billion freight industry is heavily fragmented; nine out of 10 trucks on the road belong to small trucking companies, a product of the industry’s low barriers to entry and historical resistance to consolidation. Even before the Covid-19 pandemic, this presented all kinds of logistical roadblocks to improving the industry’s overall sustainability; but today, with supply chain strategy in the spotlight, Convoy has risen to the challenge of bringing freight into the future.
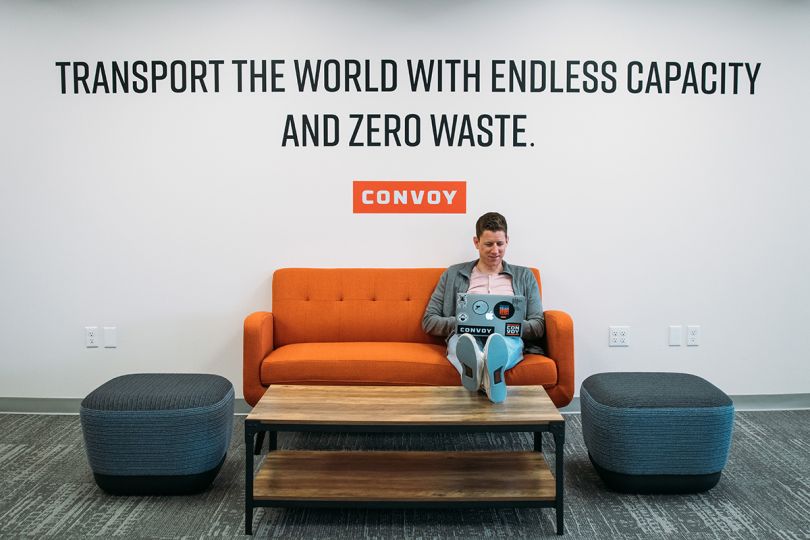
The Seattle-based company makes a difference by introducing new technologies that make freight’s supply chains more dynamic — a multi-tiered mission in an industry that, a decade ago, had truckers relying on paper driver logs and only sporadically equipped drivers with smartphones. Convoy’s digital freight network utilizes machine learning, automation, and mobile technology, all in an effort to modernize what has been a historically inflexible business.
The company has made significant in-roads toward its goals of decreasing costs for shippers, increasing earnings for carriers, and reducing carbon emissions since its founding in 2015. Fortune 500 shippers like Anheuser-Busch, Procter & Gamble and Unilever rank among Convoy’s most noteworthy customers, and investors including Bill Gates, Jeff Bezos and Bono of U2, among others, are supporting the company in their pursuit of transforming one of America’s most historic industries. And in April 2021, Convoy raised an additional $260 million in funding, valuing the company at $3.8 billion.
By leveraging a platform that itself already achieves net-zero carbon emissions, Convoy’s out to benefit the planet as much as it benefits shippers and carriers — and that collective greater good is one of the company’s key selling points.
“You shouldn't have to make a trade off between being green or paying reasonable rates to the carriers,” explained Jennifer Wong, the company’s head of sustainability. “You should be able to find more innovative solutions that are actually beneficial for all.”
This ethos has driven Convoy since the beginning and informed its most widely adopted initiatives, which leverage technology and data to cut down on waste and inefficiency while materially improving the lives of truckers.
“Our greatest impact is to be able to partner with both customers and truck drivers to be able to help make the trucking industry more sustainable,” said Wong. “We always see sustainability as a top reason for why someone chooses to join Convoy. They want to be able to make an impact, and the impact that we can have in the trucking industry is massive.”
That’s not just talk: last year, Convoy released its first corporate sustainability report, revealing that it had eliminated more than 2 million pounds of carbon emissions from mid-2019 through the end of 2020. Even more ambitiously, it vowed in the same report to prevent millions of additional pounds of carbon emissions in 2021 alone. To date, Convoy has saved more than 8 million pounds of carbon emissions from polluting the planet. Recently, Convoy also joined The Climate Pledge, a commitment co-founded by Amazon and Global Optimism, where signatories commit to reaching net-zero carbon emissions by 2040, while measuring and reporting greenhouse gas emissions, implementing decarbonization strategies, and neutralizing any remaining emissions with offsets.
According to Wong, making freight more sustainable is not only possible on an industry-wide scale but is also feasible in the near-term. That distinction matters to Convoy’s customer base, which encompasses Fortune 500 brands concerned about sustainability, as well as companies in earlier stages of making commitments to reduce their environmental footprint.
“Even if it’s incremental, any progress in sustainability is good progress,” said Wong. “You want to look at what you can do short term in addition to where you can start investing today that will drive those long-term impacts that you also want to see.”
Addressing logistical inefficiencies in freight is the most direct route to getting there. Arpan Sinha, the company’s director of product, sees his position in this respect as twofold.
“My teams sit at the nexus of supporting Conway’s two missions,” Sinha said. “How do we create endless capacity in this industry by increasing carrier productivity, and how do we reduce waste in the industry by making carriers more productive and making other partners in this ecosystem operate in a more effective manner?”
Take the problem of those dreaded empty miles, for instance. One of Convoy’s signature solutions, the Automated Reloads program, automates the process of matching loads to trucks, algorithmically bundling shipments so that carriers can keep their trucks full without hunting across multiple brokers or driving empty between loads. So far, Automated Reloads has been a success in terms of sustainability; Convoy estimates that it yields an average 45 percent decrease in CO2 emissions. And where empty miles are concerned, it reduces the industry standard of 35 percent to 19 percent, an efficiency that could lower CO2 emissions by 40 million metric tons if implemented across the industry.
Beyond its environmental value, automated matching has benefitted truck drivers who’ve been historically marginalized in freight, from female drivers to those for whom English is a second language. “From the carrier’s perspective, it removes the information asymmetry that has historically plagued this industry,” Sinha said. “Previously, you had to know where the work was. Now, all the work is posted in our app, so you as the truck driver have access to more freight in a more transparent way. It democratizes access.”
In this way, Convoy’s platform makes it easier for smaller trucking companies to plan ahead, book multiple loads in advance, and have greater certainty around revenue. A dynamic pricing engine operates along similar lines, accounting for a wide range of variables that determine costs of trucking jobs in order to get the best pricing for shippers while ensuring carriers are paid promptly and appropriately. The platform also uses predictive analytics to match shippers with a network of several thousand sensor-enabled trailers.
Improving supply-chain visibility has been a focus of Sinha’s work at Convoy from the start, but the pandemic especially stressed its importance — and exposed the brittleness of a broker-reliant system, like that which has long been prevalent in freight, and which Convoy is working to improve.
“One aspect of being a sustainable company is building resilience,” Wong said. “A lot of companies today are looking at the resiliency of their supply chains, due to the broken factors that the pandemic caused. People take for granted how easily they can get their goods. If you work in the industry, you realize there are so many dependencies.”
As customer demand soared for essential products like hand sanitizer and toilet paper, grocery stores struggled to keep shelves stocked, and online shipping delays stacked up. Throughout it all, the freight industry kept on trucking, through ever-shifting conditions — from restricted imports to health concerns and driver shortages — which pressure-tested supply chains on an unprecedented scale.
“The most important thing that we could do as a society was to stay still,” Sinha said. “Literally, that was the guidance: stay at home, don’t go anywhere. The reason why many parts of society were able to actually stay still was because the supply chain allowed us to. I think that is a really profound thing to recognize: that the most important thing that we could do was to not move, and everything else around us that was moving allowed us not to.”
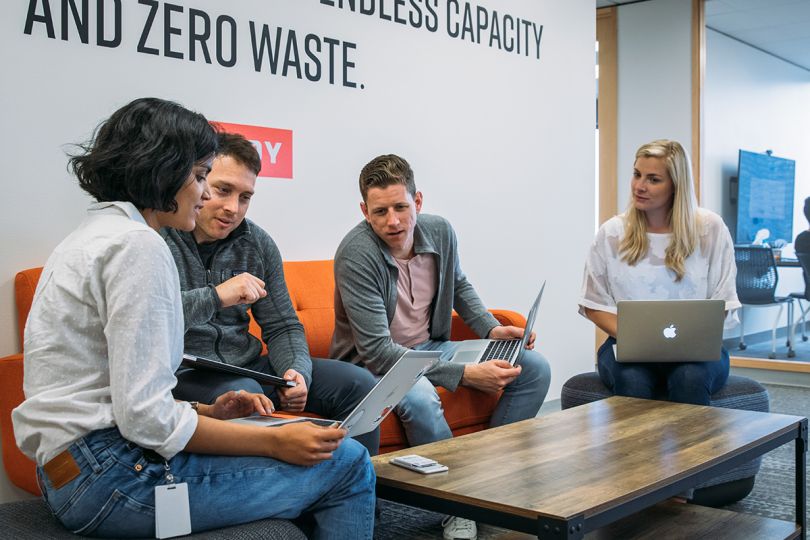
Aaron Terrazas, Convoy’s director of economic research, also remembers those early pandemic days vividly; he believes the response to supply chain disruptions missed an essential component of the crisis.
“When you think about all of the challenges that are facing the global supply chain at this moment, it is a headline issue,” Terrazas said. “This is a topic that the White House brings up.”
Often, however, forums on inflation and supply-chain disruption lead into discussions of labor shortages and decreases in vehicle availability brought on by semiconductor shortages. Policy conversations, meanwhile, can coalesce around the topic of adding more drivers and more trucks. Terrazas argues that Convoy has instead zeroed in on a better, backdoor solution: improving productivity.
“Making more of the resources we have — helping drivers do more loads in a day so that they earn more and waste less time, while increasing the utilization of their vehicles — is the fastest, least resource-intensive way to address these shortages,” Terrazas said.
As part of automated matching, Convoy broadens access to “drop-and-hook” freight, the trucking industry’s term for when a driver is able to drop a full container at a facility then hook their tractor up to a pre-loaded trailer at the same facility. Reducing transportation costs for shippers and increasing potential earnings for carriers, this “grab-and-go” approach saves time for all involved — especially compared to the “live load” approach through which drivers arrive at a facility and idle while waiting for workers to load and unload freight.
Last year, the American Trucking Association estimated that truck driver shortages would hit a historic high of 80,000 drivers; that figure represents the difference between the number of drivers currently in the market and the optimal number of drivers based on freight demand. It sounds like a steep figure, but Convoy’s efficiencies have demonstrably helped to close the gap.
“Every one percent of freight volume that transitions to the drop-and-hook model nationwide is like adding 10,000 drivers to the labor force,” said Terrazas, citing the added capacity and driving hours this efficiency unlocks. ”You can imagine a world where, with relatively small shifts in volume from live loading to drop-and-hook, you meet those very large estimates of trucker shortages in this country.”
Working at Convoy means contending with complex, real-world problems, but that’s all part of the appeal.
“You have to be excited about the ambiguity of the problem space,” Sinha said. “We don’t have all the solutions, but we are actively trying to figure out the solutions. You have to be comfortable with that intellectual and technical struggle to come up with solutions that don’t exist yet.”
Still, Convoy’s employees believe that freight is moving in the right direction. “Doing more with the resources we have is fundamentally sustainable,” concluded Terrazas. “That’s progress.”